一 The basic knowledge for CNC Machining
(一) What is CNC machining?
CNC machining process is a computerized numerical manufacturing process in which the codes and pre-programmed software control the movement of the production equipment.
A large number of complex machinery is controlled by CNC machining.
The complex machinery may include turning mills, lathes, and grinders that help cut and create different prototypes and parts and give them a definite shape. CNC machines perform all the operations of CNC machining.
(二) What is the history of CNC machining?
John T.Parsons (1913-2007) is the precursor of the modern CNC machine and the pioneer of numerical control. He is considered the father of the 2nd industrial revolution for his demanding work. He was known well due to the manufacturing of the complicated blades of helicopters.
Later, he realized that the next manufacturing level must be connecting machines to computers for various useful purposes. He manufactured the CNC manufactured parts present in different industries throughout the world. A strong national defense, cost-effective materials, and an excellent living standard are all due to the CNC machines.

(三) Development Stages

There are three developmental stages of the CNC machining process.
1: Micromachining
it is used to manufacture smaller parts less than 0.015″(0.381mm) in diameter. It is used to manufacture small parts that can measure millimeters or micrometers.
Micromachining has three types.
- Physical micromachining
- Chemical micromachining
- Mechanical micromachining
Benefits
Micromachining can easily produce the parts with micro features, reducing the lead time. The tiny components with tight tolerance and high precision can be produced by micromachining.
Applications
Micromachining is used in different industries to manufacture various components such as particle filters, medical parts, electronic components, etc.
2: Rapid prototype machining
It is a process in which a physical part of an assembly is fast fabricated using computer-aided designs. 3D printing is used to complete the creation of a part or assembly.
Different manufacturing technologies and processes are used in rapid prototype machining. Additive manufacturing is among the most commonly used technologies. Followings two processes used in rapid prototyping.
- Compressive
- Subtractive
Benefits
Rapid prototype machining could machined the parts with very fast speed, even finished in 1 working day.
Meanwhile it is a way to make the idea into the reality,then if there is some design mistake, it is very easy to find it.
Rapid prototype machining could make diversity material,from metal to plastic, from soft to harden.
Applications
It is used in many industries,such as medical industry,mechanical engineering,electronics,footwear design.
3: Precision ultra-precision machining
It is used to handle the emerging and difficult-to-cut materials or parts with great surface quality and tolerance. It helps in the production of small 3D features with higher accuracy.
Applications
Precision ultra-precision machining is widely used in the manufacturing of equipment and prototypes. Complex geometries with less installation space can create by using this machining. It is widely used in medical technology.
(四) Common CNC machine types
A wide range of CNC machines is used in CNC machining. The followings are the most common types of CNC machines.
CNC milling machines
CNC milling is the most common type that helps cut and drill using build-in tools. The material to be drilled or cut is put inside the machine, and then cutting, or drilling is done according to the computer instruction. These are available in 3-6 axis configurations.
CNC milling machine is widely used to produce the gears such as spur gear, drilling the workpiece bore, and manufacturing slots.

CNC turning machines
CNC turning machines process material to get certain specifications by following instructions in the coded program. These codes are then converted to the electrical signals responsible for activating the turning motor present in the machine.
After programming, there is no need for any operator controller in the entire process.
It is a cost-effective machine that increases the machining process’s efficiency and production time.
CNC turning machines process material to get certain specifications by following instructions in the coded program. These codes are then converted to the electrical signals responsible for activating the turning motor present in the machine.
After programming, there is no need for any operator controller in the entire process.
It is a cost-effective machine that increases the machining process’s efficiency and production time.
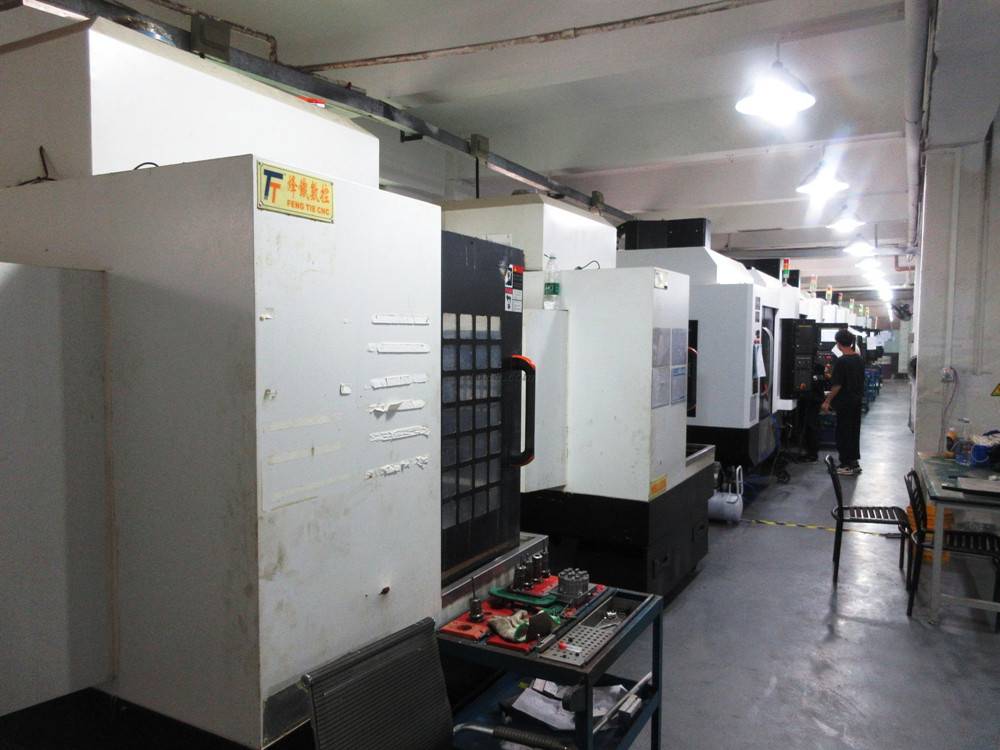
Electrical discharge machine
EDM (electrical discharge machine) is also termed a spark CNC machine that gives the material a desired shape by using an electric spark. The electrical sparks degrade the metals from the desired site and thus shape into the desired form.
The material is placed between the two electrodes. The electrical sparks are produced by electrodes which are controlled by the computer.
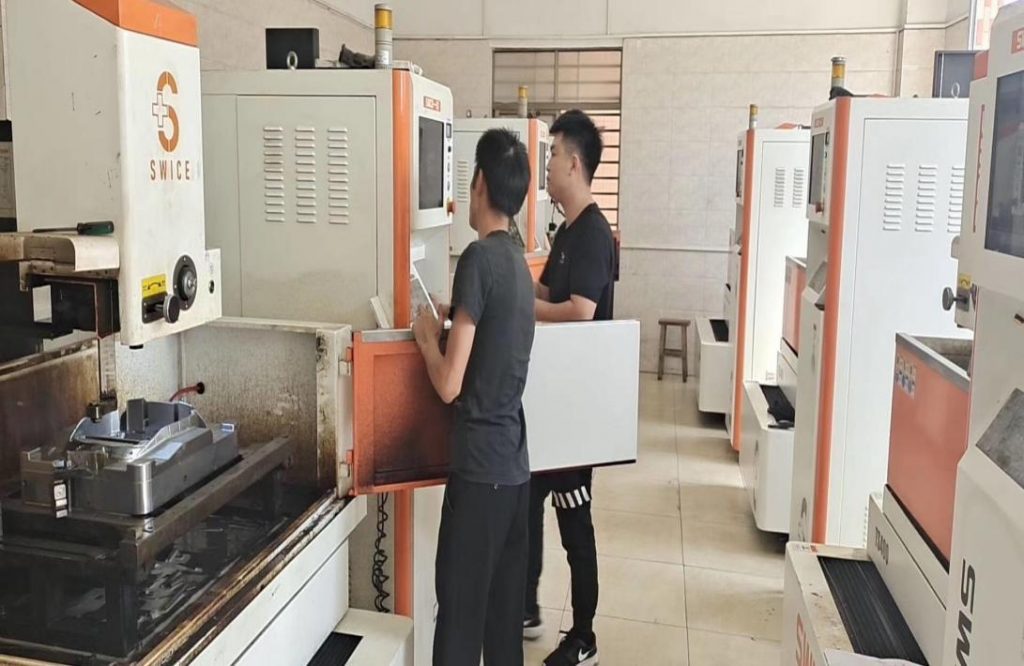
Swiss Lathe machine
Swiss Lathe machine works by turning the material during the machining operation. A lathe is present in the machine’s center, responsible for managing and transferring the material programmatically to the computer.
5-axis machine
5 axis CNC machine is a computer-operated manufacturing technique in which the cutting tool approaches the workpiece in simultaneous 5 axes in a single trip. The workpiece is attached to a rotary table that positions the stock material into the required angles.
This helps the wide range of cutting tools remove the material from the stock. This advanced machining technique operates on three linear (x y and z) and two rotational (b and c) axis rotating around the linear ones simultaneously. A 5 axis machine is a must-have for industries in different sectors.

(五) How does CNC machining work?
The CNC machines work by manipulating a wide range of tools around a different axis that varies in number. The computer programs controlled the working of the CNC machines. Thus they work by following the same information given by the computer programs. CNC machines can produce many high-precision parts with greater speed and accuracy.
For example, The CNC milling machine uses different rotating cylindrical cutters that can move on a different axis. It helps in creating the holes and slots in the operating material. It operates on 3 to 5 axis, and instructions given by the computer program controls the whole work.
Moreover, the CNC machine working mechanism is divided into four stages.
1- Creation of CAD design
CAD software is used to create computer-aided designs in 2D or 3D format.
2- Conversion of CAD file to a CNC program
It involves the conversion of the CAD files to the CAD-compatible file format. The programming codes are generated as the CNC program analyzes the CAD files.
3- CNC machine set-up
The third stage is setting up the machine. The direct fixing of the workpiece does it into the machine. The required components and tools are attached to the machine.
4- Operation execution
The operation is done by executing the running CNC program, which controls the CNC machine. The program analyzes the CAD files to ensure the making of desirable designs.
(六) Common machining processes
CNC machining mainly involves two processes.
- CNC milling process
- CNC turning process
1- CNC milling process
This process involves the use of rotating cutting tools to cut the workpiece. The workpiece is fed directly in the rotation of the cutting tool. The direction of feeding is always in the direction of the rotation of the cutting tool.
The following operations are involved in the CNC milling process.
- Peripheral CNC milling
It is used to cut deep cavities present on the workpiece. - Flat milling
It is used to cut flat-bottomed cavities, flat surfaces, and shallow surfaces.

2- CNC turning
It is a process in which parts of a workpiece are removed as it rotates on a single axis. CNC turning involves the following operations:
- Thread cutting
- Facing
- Grooving
- Boring

Some other CNC operations are as follows:
- Grinding
a process uses the grinding wheel to improve the surface roughness and remove the tool marks.

- Broaching
a process uses a broach to process various forming surfaces of workpieces. - Drilling
- Honing
- Sewing
(七) CNC machining tolerances
It is the measurement that tells about the precision level of a manufacturing part. It shows the degree of variation allowed in the final dimension of a part.
CNC machining tolerance is divided into the following types.
1: Bilateral tolerances
Bilateral tolerance indicates that the deviation from the provided dimension can be negative or positive(+/-), which can be a little smaller or bigger. It is mainly used for exterior dimensions. For example +0.015mm/-0.015mm. Which means that the manufactured parts can be smaller than 0.06mm but can not bigger than 0.06mm.

2: Unilateral tolerances
It indicates the deviations in a single direction that can be negative or positive. The example of unilateral tolerance is +0.00/-0.02mm, which means that the manufactured part can be smaller than 0.06mm but cannot exceed the valve.
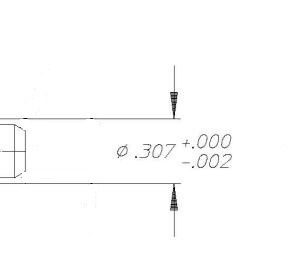
3: Standard tolerances
These are mostly used for the fabricated parts, threads, pins, pipes, etc. The CNC machining tolerance charts can use to find standard tolerances. Different international standard bodies set the standard machining tolerance range.You cuold follow the ISO2768 standard.
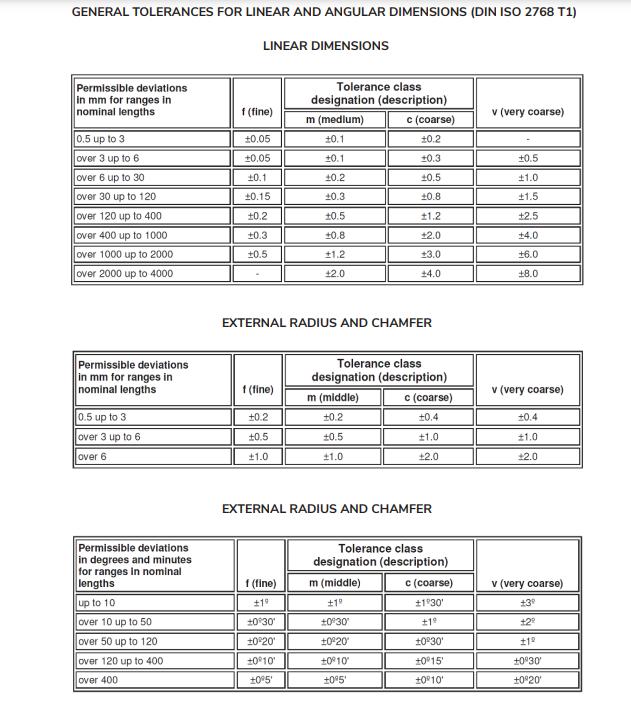
4: Limit tolerance
Limit tolerances are shown as a wide range of values, as the part’s length is the same as the measurement, ranging between 13 to 13.5mm. It means that the measurement of the part must be between the lower and upper limits.
5: Geometric dimensioning and tolerance
It is a type of tolerance that mainly highlights the allowable deviations and the measurement. This tolerance outlines the definite geometric characteristics of the various machined parts. It is mostly used for those parts having precise dimensions.
(八) CNC machining applications
As we know, CNC machining is a cost-effective and versatile manufacturing process. Thus it is widely used in different industries throughout the world. In these industries, it is used to manufacture different parts and components. The following industries widely make use of CNC machining.
1: Automotive industry
CNC machining is mostly applied in the automotive industry for production and prototyping. It also involves machining the extruded into the valves, cylinder blocks, axels, gearboxes, and many other components.
At the same time, the plastics are machined into the components like gas gauges, panels, and dashboards.
2: The defense industry
In the defense industry, prototyping is mainly used for prototyping components like reliable parts and rugged, etc. The main purpose of matching the parts is to make them capable of withstanding wear and tear.
3: Aerospace industry
CNC machining can use for a wide range of aerospace industry parts. The metal-air craft components are machined through CNC machining at high precision. A wide range of engineering metals used for CNC machining in the aerospace industry provides a lot of options to engineers.
There is a large reliable range of CNC machining applications in the aerospace industry. The fuel excess panels, fuel flow components, engine mounts, and landing gear components are machinable aerospace components.
4: Consumer electronics
It also aids in producing and prototyping a wide range of consumer electronics. These consumer electronics include smartphones, laptops, and other electronic devices.
The CNC machining aids in creating fixtures, housings, PCBs, jigs, and many other components in consumer electronics.
(九) Benefits and Limitations of CNC machining
The CNC machining process has a large number of benefits. Therefore this process has various applications.
Benefits of CNC machining
Some common CNC machining benefits are as follows:
1: High degree of automation
The main benefit of CNC machining is that it provides a high degree of automation. Such high degree of automation increases the manufacturing process’s speed, consistency, and efficiency.
2: High efficient
The process of CNC machining is a highly efficient process than other processes. It makes it more beneficial as compared to the other manufacturing processes.
This process provides great efficiency by manufacturing the desirable parts with much accuracy. It produces the parts with no or very less chances of errors in the manufacturing part.
3: Parts with complex surfaces can be machined
The manufacturing of the parts with complex surfaces makes this process much more beneficial. This process can even manufacture the parts with complex geometries that are impossible to manufacture by using other processes.
The manufacturing of parts with complex geometries allows the use of this manufacturing process at a high level.
4: High processing precision and stable quality
CNC machining is a highly precise manufacturing process that helps produce parts with stable quality. High precision provides the long service life of the process.
It also results in less energy consumption during this process. Moreover, this manufacturing process helps produce stable parts of high quality.
5: Conductive to development and improvement of new products
CNC machining is more beneficial than other processes because of the formation of new products from different ideas. Simply, it brought different ideas to new parts or components. It also brings improvements to the new products by doing useful changes.
Limitations of CNC machining
We know that the CNC machining process produces stable, accurate, and highly precise parts with very little or no possibility of error in manufacturing parts. Besides all the benefits of this manufacturing process, it also has various limitations. Here are some of the limitations of CNC machining.
1: Large investment
One of the limitations is the large investment in the machining process. The machines used in the process require a high initial investment. There is a high cost for purchasing new tools and machines for this process.
2: High maintenance cost
The machining process also requires high maintenance costs. The specific tools are used to manufacture a specific part or component. This high cost is because it uses specific tools and machines to maintain the machining process.
Moreover, any damage to the manufacturing part can result in additional costs that make it an expensive process.
This process provides great efficiency by manufacturing the desirable parts with much accuracy. It produces the parts with no or very less chances of errors in the manufacturing part.
3: Need for experienced operators
The operators for the CNC machining must be highly experienced. The operators must have multi-tasking and strong problem-solving skills.
They must have knowledge about CAD software and good information about computer programming.
They must have a mechanical aptitude.
(十) Future of CNC machining
The future of CNC machining is looking for different ways to increase complexity. They are working on synchronizing different, more precise, and efficient machines and can be used for several different purposes with much complexity.
二 How to design CNC Machining Parts?
1: Cavities and pockets
The cavities and pockets are important features in CNC designs. The cavities with smaller depth-to-width ratio results in broken cutters, chip evacuation, and tool deflection. For desirable results, limit the depth cavity to four times its width. Similarly, deep pockets should avoid CNC design as they require longer tools that increase machining costs.
2: Internal edges
Internal edges should not be sharp in CNC designs. The radius of edges should be a bit larger than the cutters because if the radius of edges is similar to the cutter diameter, it may result in premature tool wear and chatter.
3: Tolerances
You must avoid applying tight tolerances to the workpiece because it results in an increased cost of the machining process. Because of tight tolerance, it may cause longer cycle time, enhanced scrap, special tools for measurement, and more fixturing.
Just apply it to specific parts where tight tolerance is compulsory for a specific design to decrease the overall cost of the machining process.
4: Small features
You must avoid machining small features in a part because the small machining features need specialized tools. Commonly, micro drills are used to machine small features such as small holes. It can greatly increase the machining time and cost.
三 CNC machining materials
(一)Metals
You can use the following metals for CNC machining.
1: Aluminium
Aluminum is a metal and is one of the most commonly used materials for CNC machining. It is an ideal metal for different mecharanical components due to its greater corrosion resistance, weldability, and better formability.
It is used in medical devices, aerospace, aircraft fittings, automotive, etc.Below table is the aluminum brands.

For more details, you could read https://www.worthyhardware.com/cnc-machining-aluminium-material/
2: Brass
Brass is a non-magnetic material used to create parts that need electrical conductivity and strength applications.
It is considered the cheapest material used for CNC machining having high corrosion resistance and low friction coefficient.
It is mostly used in engineering, medical equipment, etc.
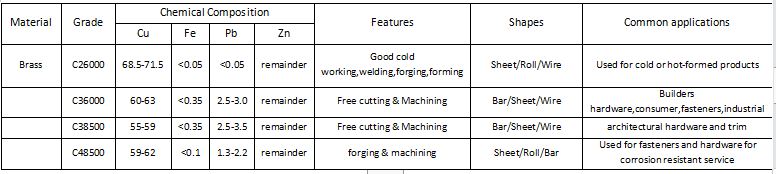
3: Bronze
Bronze is a ductile metal used for CNC machining due to its high machinability and higher corrosion resistance.
It is a combination of copper bases with different alloys. It is expensive and commonly used in industrial and marine applications.
4.Copper
Copper is a chemical element with the symbol Cu. It is a soft, malleable, and ductile metal with very high thermal and electrical conductivity.
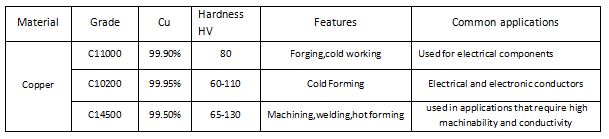
5. Stainless steel
It is a non-magnetic material having higher strength and is used to manufacture components that need higher formability and weldability.
It is used in aerospace, medical, and many household applications such as screws, machinery parts, etc.

6: Titanium
Titanium is a tough material with high corrosion resistance and greater strength. Due to its toughness, it is a bit tough to machine and requires special cutters.
It is not considered a good conductor of electricity and cannot be polished well.
It is an expensive metal used in aerospace, industrial, and military applications.
Material | Grade | Alternative names | Ultimate tensile Strength (MPa) | Process compatibility | Common applications |
---|---|---|---|---|---|
Titanium | Grade2 | TA2 | 430 | Cold forming | Equipments,Consumer products |
Titanium | Grade5 | Titanium 6Al-4V | 1170 | welding, forming and cold working | aerospace, marine, and offshore industries. |
7: Alloy steel
Alloy steel is widely used as a CNC material because outfits enhanced formability, higher strength, and great machinability.
It can be easily heat treatable and used in manufacturing components that need strong welds.
Due to its higher corrosion resistance and strength, it found applications in the aerospace and automotive industry.
Material | Grade | Alternative names | Ultimate tensile Strength (MPa) | Process compatibility | Common applications |
---|---|---|---|---|---|
Alloy Steel | 4130 | 25CrMo4 | 600 | Welding,cutting and machining | Manufacturing equipment |
Alloy Steel | 4140 | 42CrMo | 670 | machining | Aircraft engine mounts and welded tubing |
Alloy Steel | 1.7371 | 16MnCr5 | 550 | machining | Gears,worm gears and sealing bushings |
8: Tool steel
Tool steel is a hard material having high toughness and high wear resistance.
It is a tough material, and tool steel is difficult to machine.
It is most commonly used in the manufacturing of measuring tools, various cutting tools, and tools having higher resistance.
Material | Grade | Alternative names | Ultimate tensile Strength (MPa) | Process compatibility | Common applications |
---|---|---|---|---|---|
Tool Steel | D2 | Cr12Mo1v1 | 2100 | machining | Blanking, forming, and trim dies |
Tool Steel | S7 | 5Cr3Mn1SiMo1V | 2025 | machining | Blades,dies |
Tool Steel | A2 | Cr5Mo1v | 1858 | machining | Dies and tools |
Tool Steel | S235JR | Q235B | 510 | machining | Construction of industrial and residential facilities |
Tool Steel | H13 | 4Cr5MoSiV1 | 1200 | machining | Inserts and dies |
(二) Plastics
Just like metals, plastics can be machined. The following plastics are commonly used for CNC machining.
1: Delrin
It is a free-cut plastic considered best for CNC machining because of its excellent machinability and mechanical properties.
It is an ideal material for those components that need tight tolerance and complex shapes or geometries.
The Delrin uses for the applications in automotive parts, medical equipment, consumer electronics, etc.
Material | Other names | Ultimate tensile Strength (MPa) | Yield strength (MPa) | Colors | Common applications |
---|---|---|---|---|---|
Delrin | POM | 60 | 48.6 – 72.4 | Black and White | Pump,valve components and electrical insulator parts |
Delrin | Acetal | 60 | 48.6 – 72.4 | Black and White | Pump,valve components and electrical insulator parts |
2: ABS
It is a well-rounded plastic known for its high toughness and high impact strength. It can be easily machined because it can be easily welded, glued, and easily painted. It is a cheap material that is best for machining the parts that need toughness.
Its common applications include manufacturing electronic enclosures, household appliances, etc.
Material | Other names | Ultimate tensile Strength (MPa) | Yield strength (MPa) | Colors | Common applications |
---|---|---|---|---|---|
ABS | Acrylonitrile butadiene styrene | 55 | 18-50 | Multiple | Automotive applications |
3: Nylon
Nylon is a durable and strong plastic having high rigidity, high heat and chemical resistance. The rigidity helps nylon to prevent deformation, thus retaining its shape. Therefore it is considered suitable for CNC machining.
It is commonly used in aerospace components, electrical insulation, medical devices, etc.
Material | Other names | Ultimate tensile Strength (MPa) | Yield strength (MPa) | Colors | Common applications |
---|---|---|---|---|---|
Nylon | PA6 | 40 | 50-63 | Black and White | Plastic Fasteners and Machine Parts |
4: Polycarbonate (PC)
It is a transparent thermoplastic with a milky-blue appearance. It is commonly used for CNC machining and can be easily recyclable. It offers high impact strength and high transparency. It is used in manufacturing light pipes, bulletproof glass, CDs, optical disks, mobile phones, etc.
Material | Other names | Ultimate tensile Strength (MPa) | Yield strength (MPa) | Colors | Common applications |
---|---|---|---|---|---|
Polycarbonate | PC | 28-75 | 39-70 | Transparent | compact disc,safety helmets |
5: PEEK
It is a high-performance thermoplastic offering better water and chemical resistance. Because of its dimensional stability and higher strength, it is used to manufacture various industrial components.
It possesses tight tolerance and high precision.
It is used in the manufacturing parts like bearings, blocks, rollers and wheels, manifolds, etc.
Material | Other names | Ultimate tensile Strength (MPa) | Yield strength (MPa) | Colors | Common applications |
---|---|---|---|---|---|
PEEK | Polyether ether ketone | 50.3-265 | 65.0-120 | Brown and black | Oil and gas industry |
6: Teflon (PTFE)
It is a low friction engineering plastic with greater flexibility, excellent heat and chemical resistance, and a high strength-to-weight ratio.
Due to higher accuracy, it s used in the medical and surgery, mechanical components, vehicles and automobiles, and aerospace industry.
Material | Other names | Ultimate tensile Strength (MPa) | Yield strength (MPa) | Colors | Common applications |
---|---|---|---|---|---|
Teflon | PTFE | 35-40 | 9-30 | Black and White | Cookware and Machine parts |
7: Acrylic
Acrylic is among the clearest plastics used for CNC machining.
It is a durable, lightweight, and tough thermoplastic that shows high resistance to UV light ensuring high stability.
Its shows applications in the automotive industry, lighting, electronics, medical and healthcare, architecture and construction, etc.
Material | Other names | Ultimate tensile Strength (MPa) | Yield strength (MPa) | Colors | Common applications |
---|---|---|---|---|---|
Acrylic | PPMA | 62-83 | 64-84 | Transparent and black | Consumer |
8: PP
It is a thermoplastic polymer resin used widely in CNC machining.
It has a crystalline structure having greater hardness and heat resistance.
Its machining properties make it suitable for many industrial and commercial applications.
Material | Other names | Ultimate tensile Strength (MPa) | Yield strength (MPa) | Colors | Common applications |
---|---|---|---|---|---|
PP | Polypropylene | 27 | 31-45 | Multiple | Medical Applications and Consumer Products |
9: PVC
It is an engineering plastic that is considered suitable for CNC machining.
It is highly ultraviolet and moisture resistant. Moreover, it also possesses excellent insulating properties.
It is used in several medical, energy, and electrical industries and construction materials.
Material | Other names | Ultimate tensile Strength (MPa) | Yield strength (MPa) | Colors | Common applications |
---|---|---|---|---|---|
PVC | Polyvinyl chloride | 46-58 | 31-60 | Light yellow | Pumps & valve bodies |
10: PE
It is among the most commonly used plastics for CNC machining.
It is a thermoplastic having good weather resistance and greater impact strength. The plastic comes with a high strength-to-weight ratio, making for manufacturing different parts with greater mechanical properties, repeatability, and accuracy.
Material | Other names | Ultimate tensile Strength (MPa) | Yield strength (MPa) | Colors | Common applications |
---|---|---|---|---|---|
PE | Polyethylene,HDPE, LDPE, LLDPE | 15-45 | 2.7-200 | Black and White | Electrical insulation, household containers |
(三)Wood
The following woods are used for CNC machining.
1: Walnut
It is a brown hardwood known for its durability and higher strength, used in CNC machining.
It is expensive compared to other woods and is commonly used to manufacture musical instruments, sculptures, furniture, etc.
Material | Desity (kg/m³) | Cost | Source | Colors | Common applications |
---|---|---|---|---|---|
Walnut | 630 | Expensive | Amercia | Light brown to dark chocolate | Furniture, cabinets, flooring |
2: Beech
It is an odorless wood used for CNC machining.
It is heavy and much stronger, making it suitable for manufacturing different parts. Due to its even texture, it is used to manufacture many industries.
Material | Desity (kg/m³) | Cost | Source | Colors | Common applications |
---|---|---|---|---|---|
Beech | 700 | Expensive | Amercia | pale cream color | Furniture, musical instruments |
3: Oak
Oak is a wood with greater hardness and weight. Due to its hardness, it prevents breakage of products and is thus widely used in CNC machining.
It is highly weather and moisture resistant, so it is not damaged by environmental variation.
It is used in the manufacturing of ship buildings and furniture etc.
Material | Desity (kg/m³) | Cost | Source | Colors | Common applications |
---|---|---|---|---|---|
Oak | 600 | Less Expensive | China | cream color | Furniture |
4: Maple
It is considered the hardest wood with high durability. It is an ideal wood for CNC machining because it does not need any filler after machining for finishing purposes.
Due to its hardness, it is used to manufacture floor pavers, workbenches, desks, etc.
Material | Desity (kg/m³) | Cost | Source | Colors | Common applications |
---|---|---|---|---|---|
Maple | 750 | Expensive | Amercia | dust-color | High-end furniture and kitchen accessories |
5:Plywood
Plywood is a typical artificial board, also called multi-layer board.
It has a typical odd-numbered layered structure. Each layer is superimposed perpendicular to each other,so the constantly shrink and expand doest like solid wood,it is not easily deformed.
Material | Desity (kg/m³) | Cost | Source | Colors | Common applications |
---|---|---|---|---|---|
Plywood | 500 | Cheap | China | Multiple | Roofing and Flooring,Exterior Wall |
(四) Carbon fiber
Carbon fiber is a great choice for CNC machining because of its lightweight and hardness.
It is highly corrosion-resistant and thermally stable. Due to these properties, it is used to manufacture stronger parts for drones, vehicles, cars, etc.
Material | Desity (g/cm³) | Ultimate tensile Strength (MPa) | Yield strength (MPa) | Process compatibility | Common applications |
---|---|---|---|---|---|
Carbon Fiber | 1.5-1.8 | 0.917 – 3790 | 4.62 – 3220 | CNC machining | Automation and Robotics |
四. CNC machining surface finish
1: As Machined with Ra1.6μm and Ra3.2μm
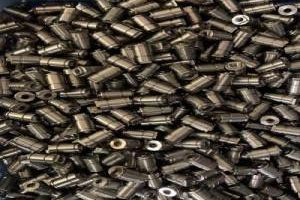
Ra3.2μm is the standard surface finish and recommended maximum surface roughness for CNC machined parts subject to vibration, loads, and stress. It can use with fine feeds, high speeds, and light cuts and is suitable for consumer parts.

Ra1.6μm recommends stresses and tight parts, but it is not good for fast rotating parts. It can produce with the usage of light cuts, fine feeds, and high speed under controlled conditions.
2: Fine machining Ra0.8μm

Ra1.6μm recommends stresses and tight parts, but it is not good for fast rotating parts. It can produce with the usage of light cuts, fine feeds, and high speed under controlled conditions.
3: Polishing Ra0.4μm
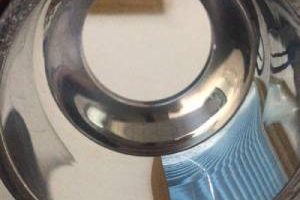
It is the highest quality surface roughness and, in technical terms, the finest and least roughness. This type of surface finish can suggest machined parts under high stress and tension and take more effort and time for the manufacturing process. It can specify when your priority is smoothness and requires rapidly rotating parts and components.
4: Brushing

It is a surface treatment process in which traces are drawn on a material surface by using different abrasive belts. The finish is affected by the thickness of these abrasive belts. Brushing is mostly used for aluminum.
5: Sand-Blasting

It is also named abrasive blasting. It is a surface finishing process in which abrasive particles are sprayed under high pressure against a surface by a powered machine. A smoother texture is created due to the strike of the particles on the surface.
6: Anodized type II

It is an electrochemical process in which aluminum oxide is the buildup on the surface as the aluminum is placed in a sulfuric bath. It results in sulphuric acid at a very low temperature by using the corrosion-resistant properties of aluminum. Its main purpose is to provide color and protection to the aluminum.
7: Anodized type II + sandblasting
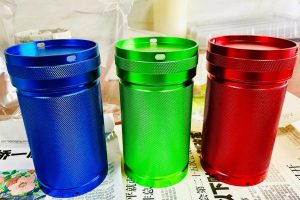
8: Anodized type III

It is a process of forming a thick coating of aluminum oxide in sulfuric acid at a very low temperature. It results in the formation of abrasion-resistant and hard porous oxide on aluminum. It makes aluminum harder and makes it heat, wear, and corrosion-resistant.
9: Powder coating

It is a surface treatment in which a free-flowing powder is applied electrostatically, and then it is cured under UV or heat light. It protects the different metals from toxic environmental factors, scratches, and rust.
10: Black oxidized

It is a process in which black iron oxide is formed on the ferrous metal’s surface. The purpose of black oxidized is to minimize the light reflection in ferrous materials and make them corrosion resistant.
11: Zinc plating
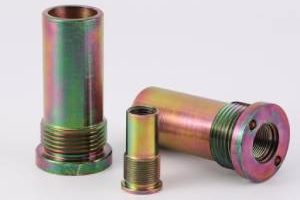
Zinc plating can involve the process in which a thin coating of metal such as of zinc metal is electrodeposited. It can coat on any other metal. Zinc plating can increase the corrosion-resistant properties of the essential metal.
12: Electroless nickel plating
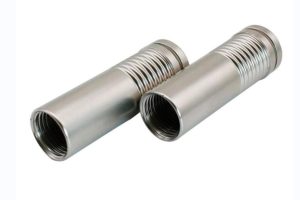
It is a process in which a controlled chemical reduction deposits a metal coating. The deposited metal catalyzes the chemical reduction. The processing of electroless nickel plating does not require an external current. It increases the corrosion resistance properties of the coated material.
13: Electro nickel plating
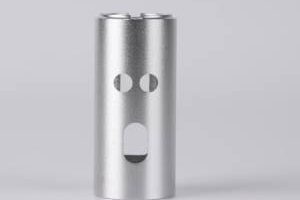
It is a process in which nickel is coated over the surface of a material. The most commonly used material for coating is metals. Electro nickel plating requires an external electric current for coating. It enhances the wear and corrosion resistance of the coated material.
14: Chromate conversion coating

It is a process in which a protective layer is formed on the metal surface by immersing the metal in a solution. A solution containing hexavalent chromium ions that react with aluminum oxides present on the metal surface. It provides a greater decorative finish and high corrosion resistance and makes it conductive.
15: Passivate
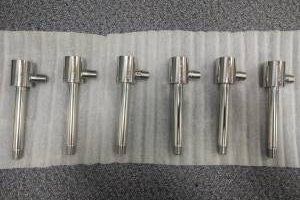
The passive process involves coating a protective material such as metal oxides on the metallic material base. The process prevents the coated metal from corrosion. If it isn’t done, then the environmental variations may damage the metallic surface.
16: Phosphate plated

In this process, a layer of water-insoluble phosphate is formed on the surface of the metal by immersing parts of steel in a phosphate solution. It not only improves the friction properties but also provides greater friction. It also protects from rust.
17: Electrophoresis
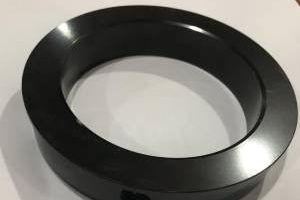
It is a process in which the field of electrical charge is used to separate charged particles. It improves the wear metals corrosion properties of metals’ adhesion properties.
18: Tumbling

Tumbling is a process in which the rough and the small parts of the metals and the plastics are polished simultaneously. It provides consistency and versatility to the polished material and gives a better surface finish.
19: Tin plating
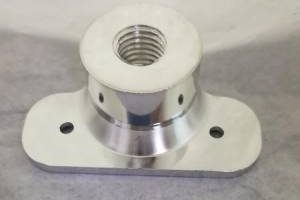
It is a cost-effective material that uses electric current for the deposition of the coating of tin plating on the surface of a metal. It provides better solderability and contact resistance and makes it highly effective for shielding.
20: Varnish wood surface
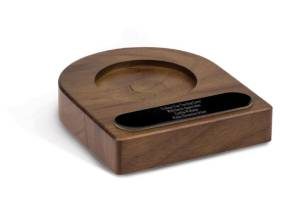
This process includes the application of a protective substance on the surface of the wood. It provides a durable finish to the wood and protects against stains, scratches, and harmful environmental factors.
21: Lacquer wood surface
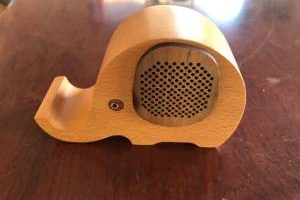
The lacquer is applied on the wood surface for fine finishing lacquer wood surface. Lacquer is a chemical, and its coating adds the attractiveness and the beauty of the wood and is not affected by the water.
22: PTFE coating

It is a high-performance, versatile fluoropolymer composed of fluorine atoms and carbon. It is most commonly used for non-stick coating of different appliances. It protects appliances against chemicals and makes them chemical resistant.
23: Gold plating
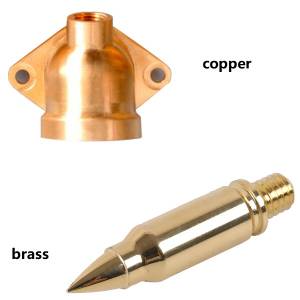
It is a method of deposition of a thin layer of gold on the surface of the metal by electrochemical or chemical plating. It increases the thermal electroconductivity of metals, makes them malleable, and protects against corrosion.
24: Silver plating

It is a process in which a thin layer of silver is coated on the surface of another metal. It provides solderability and a great surface finish. It also makes the coated metal electrical resistant.
25: Carburizing
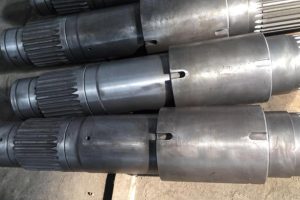
It is a hardening process that involves the diffusion of the carbon on the surface of a steel pat at a high temperature. It results in the formation of the wear-resistant layer and provides a safer and stronger material.
五. Tips to reduce the machining cost
1: Choose qualified tools
Choosing the right tools is very important in the CNC machining process. You must choose the tools according to the cutting of the materials.
Choosing qualified tools helps in the high performance of the machining process.

2: Choose the suitable material
The process of CNC machining greatly on the material you select for CNC machining.
A large variety of materials is the machining process. But you must select the best material for manufacturing your desired product.For more details, you could read the above about each material.
3: Avoid thin-walled parts
You must avoid using thin-walled parts for the manufacturing of your workpiece. The thin walls can be easily bent and deformed, thus resulting in the deformation of your workpiece.
4: Avoid small tolerances
Small tolerances should avoid during the process of CNC machining. The small tolerances may cause the malfunctioning of the workpiece.
5: Avoid many complex geometries
The formation of complex geometries should avoid during the CNC machining. The complex geometries increase the machining time and increase the cost of the machining process.
6: Avoid small radius
The small radius is not recommended in CNC machining because it results in the poor surface finish of different parts formed in the CNC machining.
7: Less surface treatment
The surface treatment should be less in CNC machining. More surface treatments may increase the thickness of the walls of parts, thus resulting in the malfunction of parts. It also increases the cost of the machining process.
8: Avoid deep pockets
The formation of deep pockets should avoid during the machining process because it can cause tool breakage. It may also increase the machining cost and time.
9: Keep round inner corners
In CNC machining, the inner corners should keep around because they are not only appealing but also helps in the easier processing of information during machining.
10: Use standard drill points
A standard drill point is recommended in various cutting operations during CNC machining. It helps you in saving money during the machining process.
11: Order a big quantity
It is the best way of reducing the cost of the CNC machining process. Ordering a large volume of different parts helps reduce the cost of the parts per unit. So, it makes your machining process cost-effective.
12: Reduce the scrape rate
The production of scrape directly affects the efficiency of the CNC machining process. So reducing the scrape rate can increase the efficiency of the machining process.
13: Trained the experienced workers
The experience workers should train to manufacture definite parts in the CNC machining. Only the trained workers can manufacture the desired product with accuracy.
14: Optimize the machining process
Optimizing the machining process helps you in increasing the performance of the machine. It helps in the manufacturing of particular parts and increases the efficiency of the machining process.
15: Reduce the set-up time
It is the best option to reduce set-up time in CNC machining. Reducing set-up time helps in reducing the batch sizes and the lead time of the CNC machining.