What is hard anodizing?
The process of hard anodizing is similar to anodizing. It is to reduce the dissolution rate of the film when aluminum part is anodized and obtain a thicker and denser anodic oxide film. This more thickness could improve the corrosion resistance, wear resistance, weather resistance, insulation and adsorption of aluminum parts.

Benefits for hard anodizing?
High hardness: after hard oxidation of aluminum alloy, the surface hardness can reach up to about HV500.
The thickness of the oxide film is 25-250 microns;
Strong adhesion: According to the characteristics of oxidation generated by hard oxidation, 50% of all the oxide films formed penetrate inside the aluminum alloy, and 50% adhere to the surface of the aluminum alloy;
Good insulation: the breakdown can reach 2000V;
Good abrasion resistance: For aluminum alloys with a copper content of less than 2%, the maximum wear index is 3.5mg/1000 revolutions;
Non-toxic: The oxide film and the electrochemical process used to produce the anodic oxide film are harmless to the human body.
Difference between hard anodizing (MIL-A-8625 Type III) & common anodizing (MIL-A-8625 Type II)
Different thickness: The thickness of hard anodizing is thicker than that of ordinary oxide. Generally, the thickness of ordinary oxide film is 8--12 um, hard oxide film is generally 40-70 um.
Unreasonable hardness: Normal anodizing is generally HV250-350, and hard anodizing is generally HV350-550.
Different temperature: Normally the temperature for common anodizing is around 18-22℃, however for hard anodizing is only below 5°C.That is to say, the lower the temperature, the higher the hardness.
Different Aluminum Hard Anodized color projects
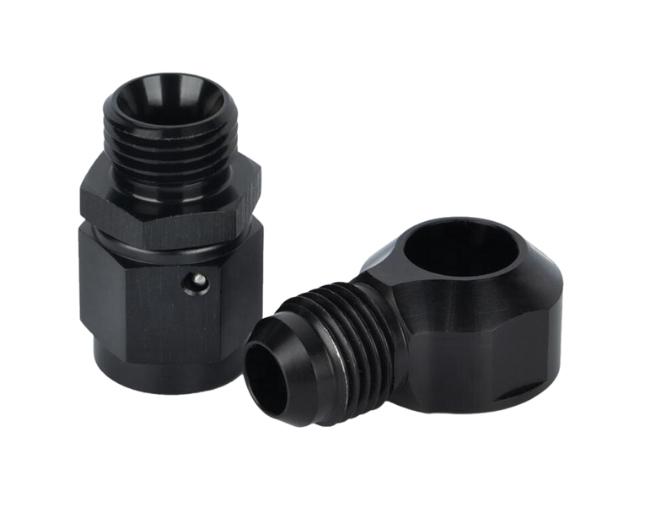
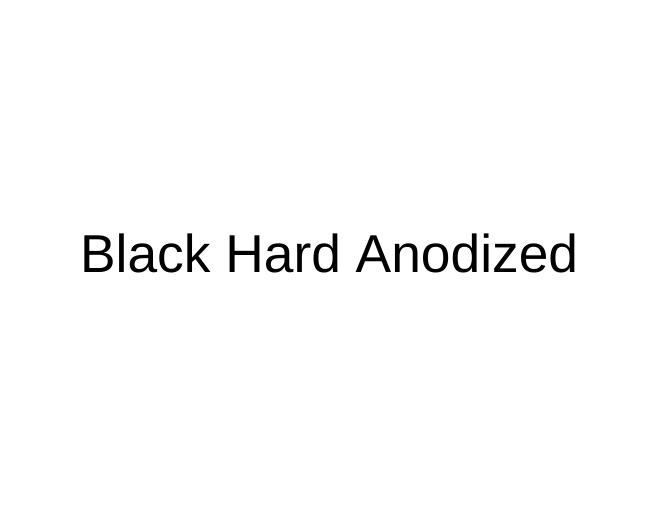

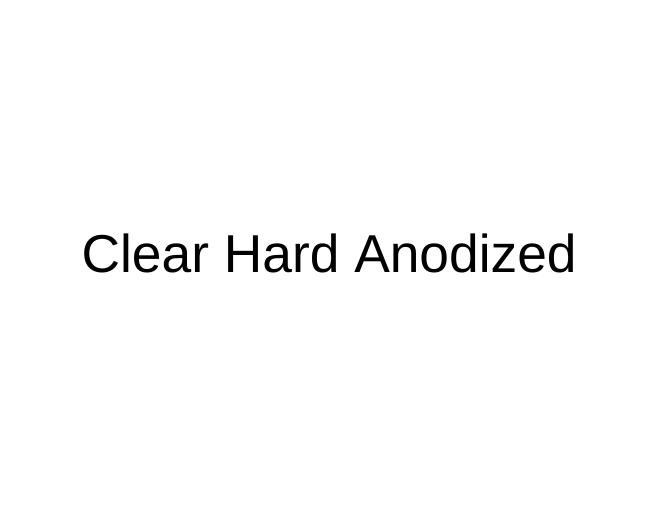
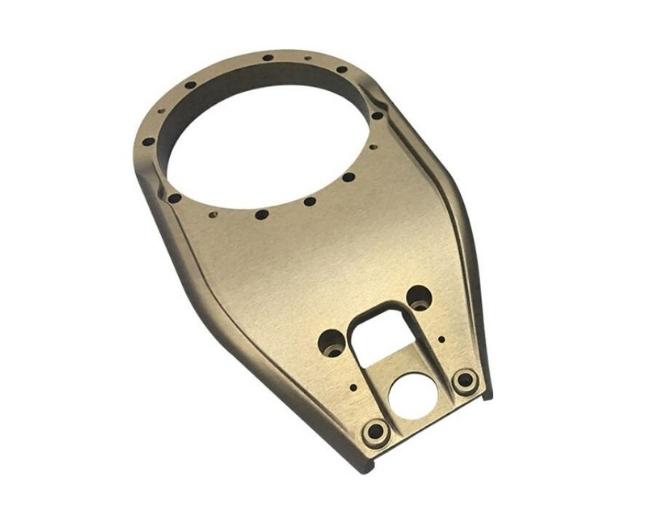
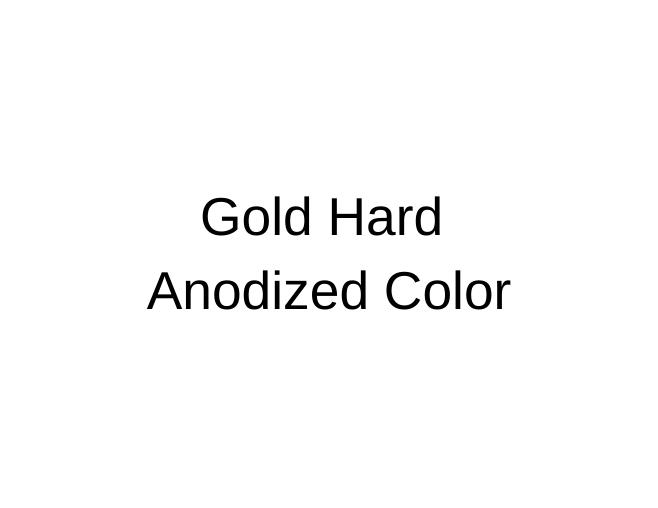
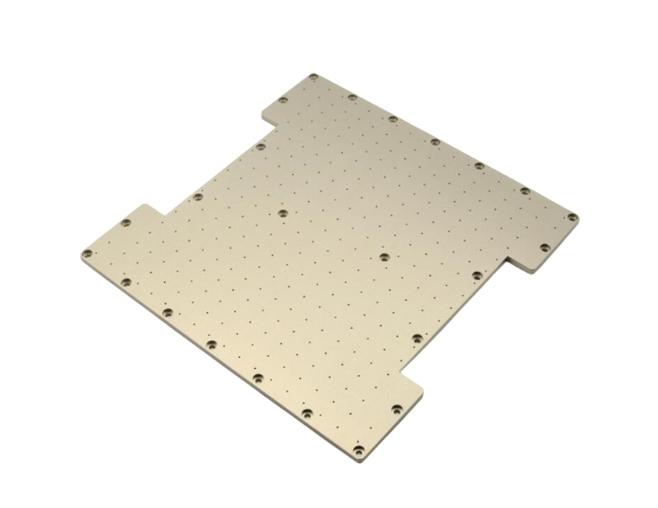

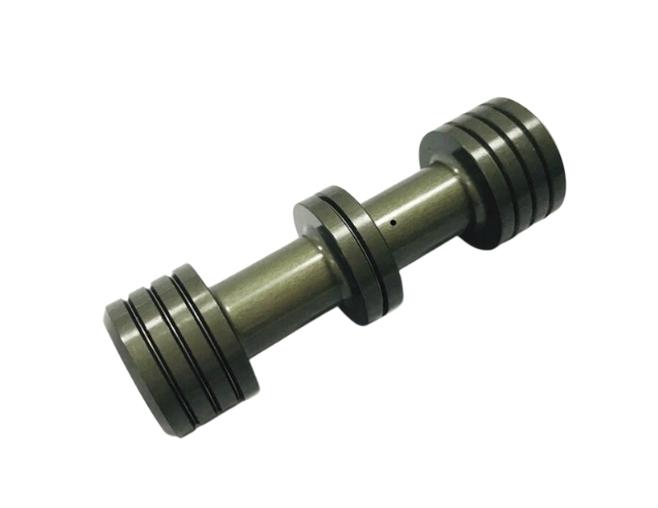
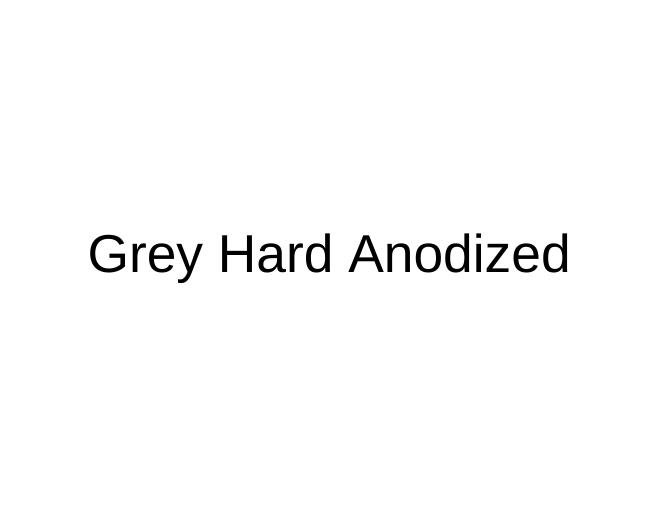
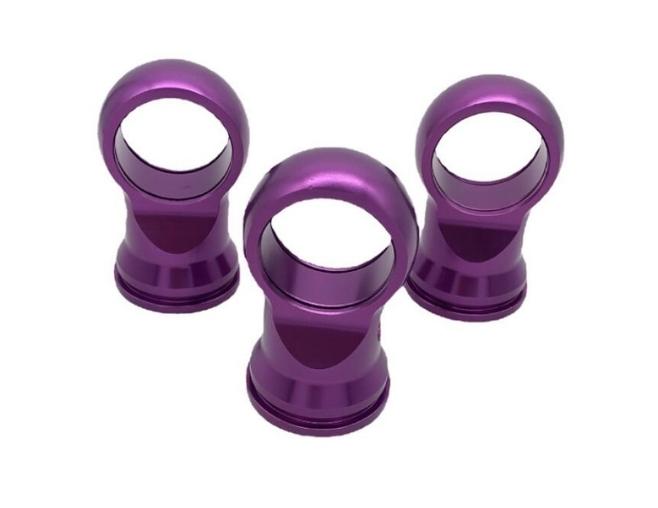

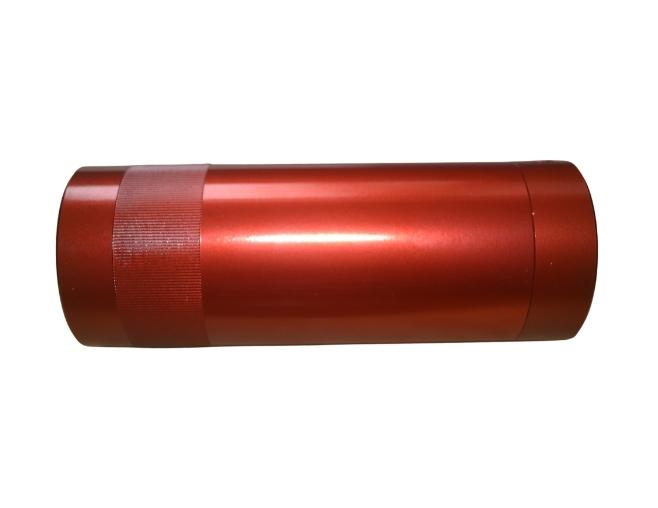


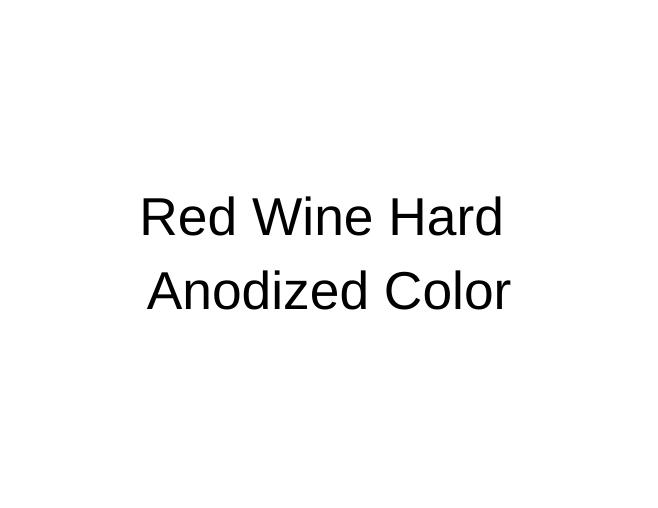