Our CNC Machining Service
Whether you would like to buy 1 pcs prototype, or want to buy 50-100 pcs small batches for trial production, or want to put the product into mass production, we are an excellent choice for you. We have advanced 3 axis, 5 axis milling machine, Swiss lathe, turning and milling machine, EDM, grinding machine and up to 100 sets of equipment. We are also strong in making various materials and can work with customers to do many kinds of surface treatments, as well as final assembly of finished products.
CNC Machining Projects
We machine rapid prototypes, low-volume production and mass production orders for customers in multiple industries.
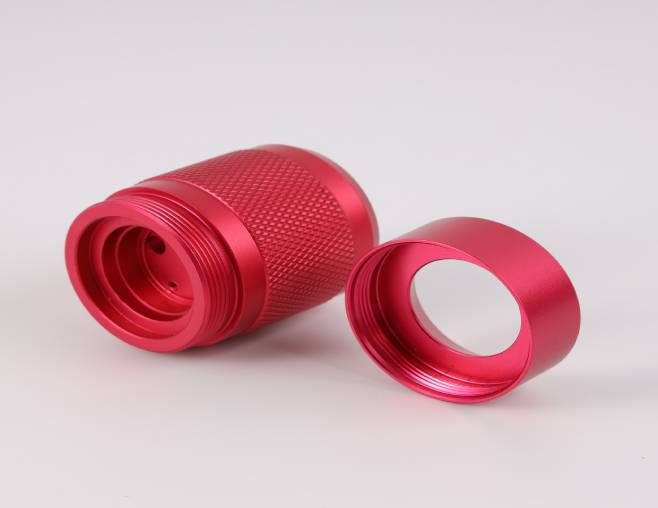
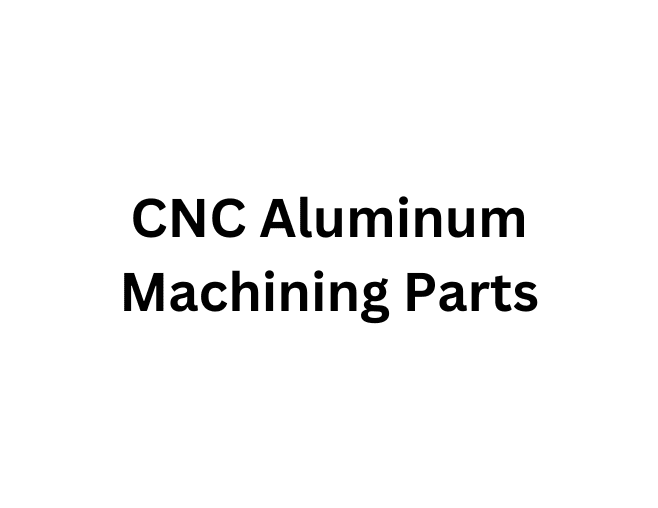
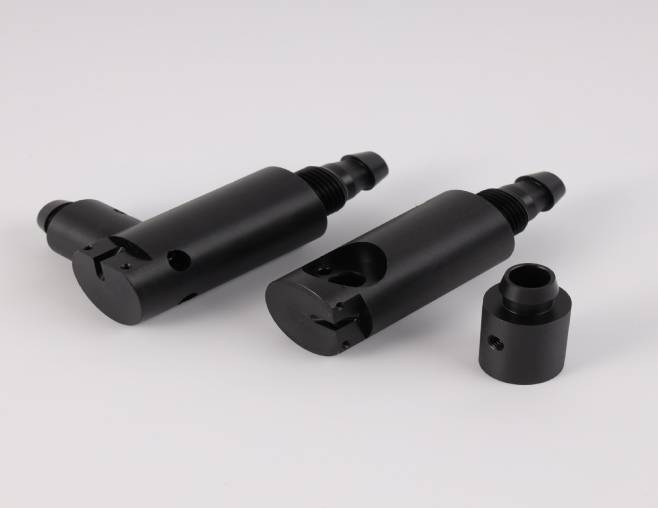
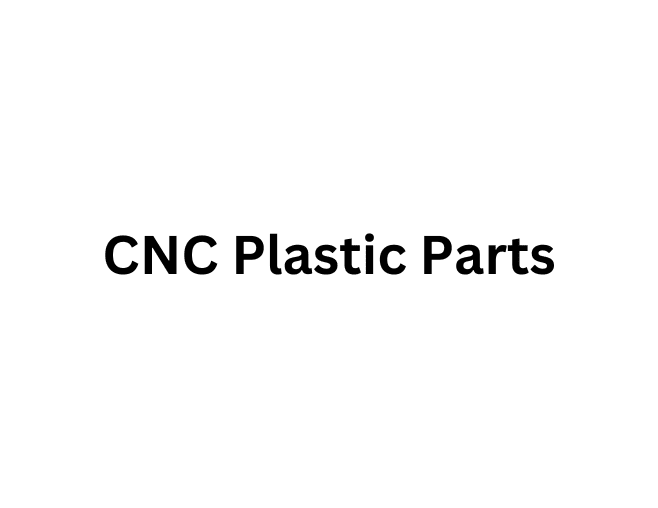
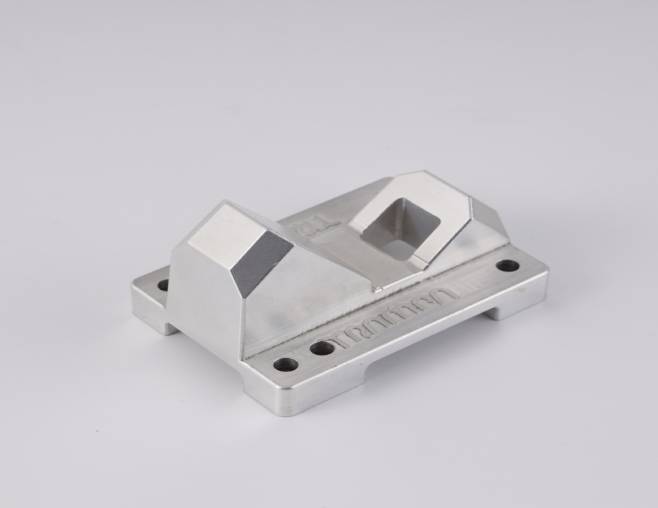

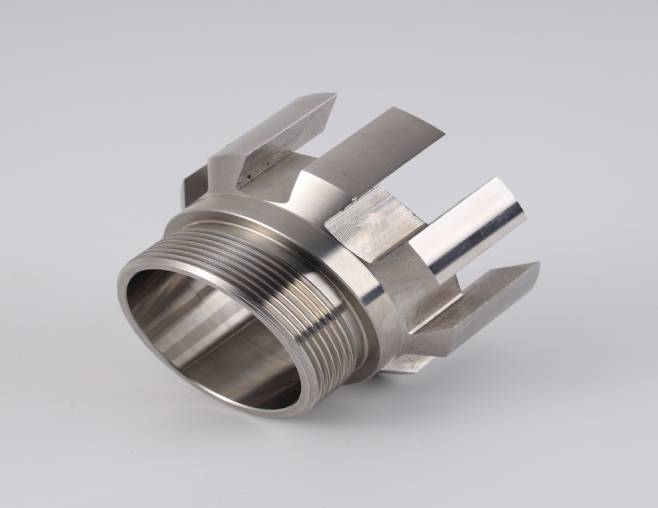
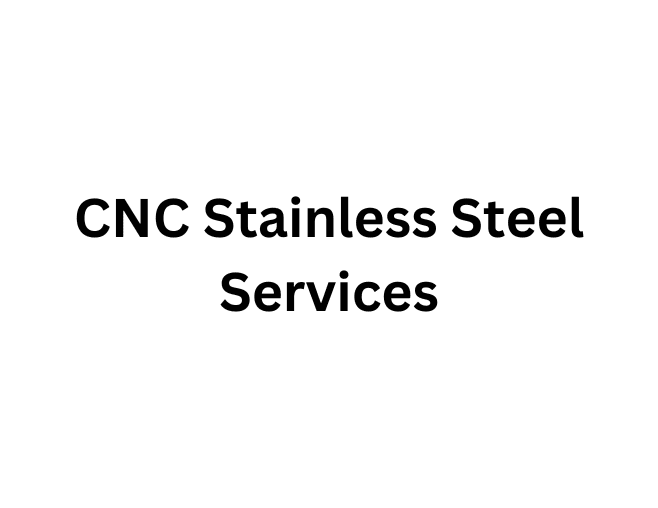
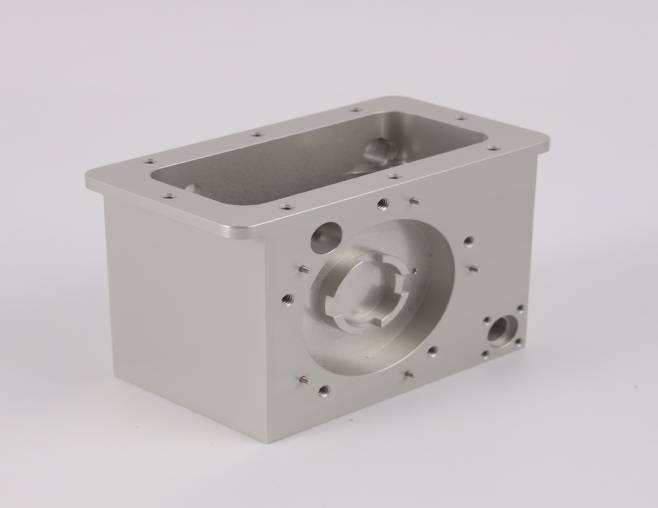
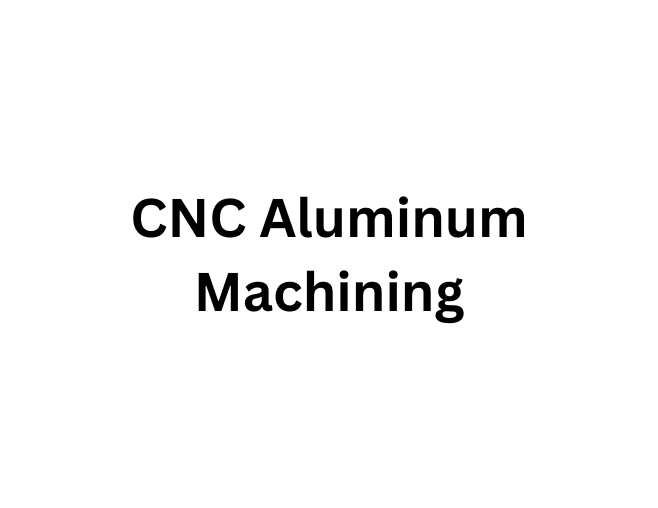
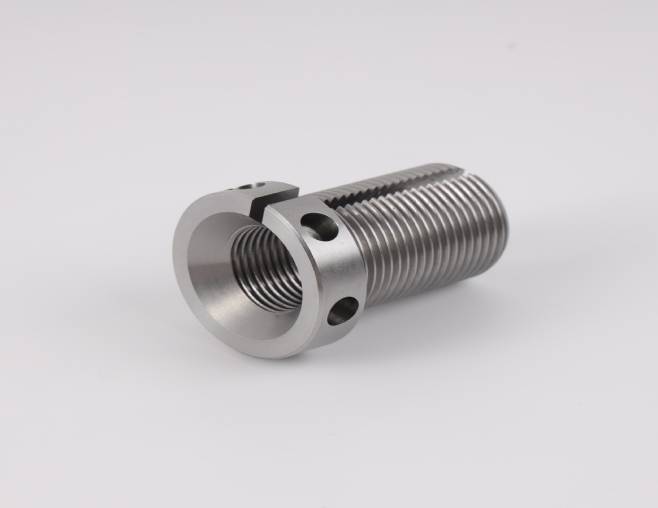
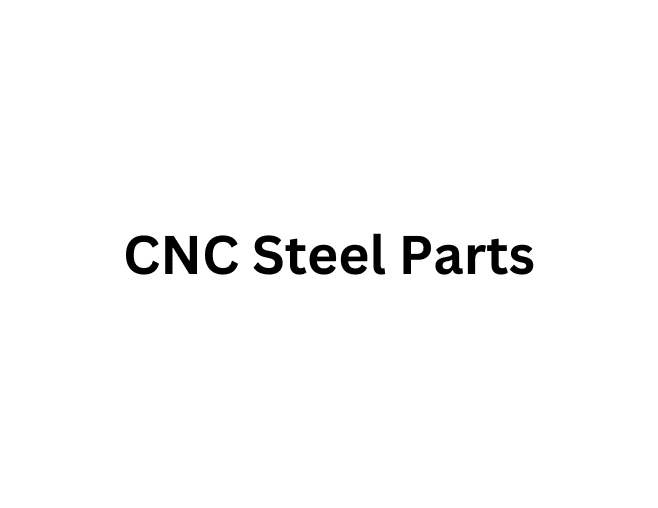
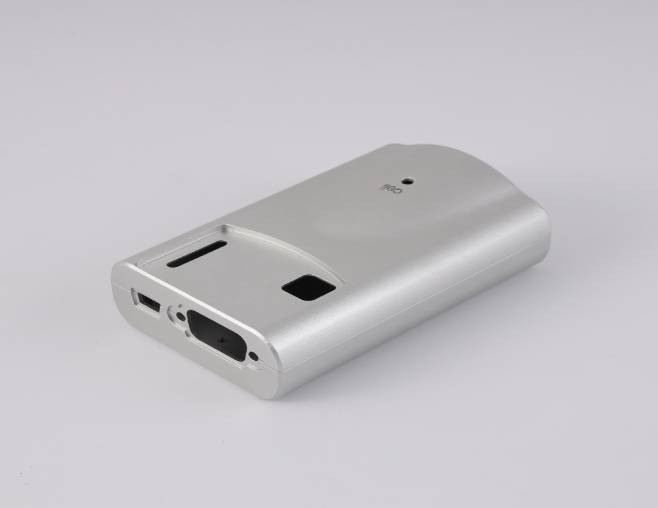
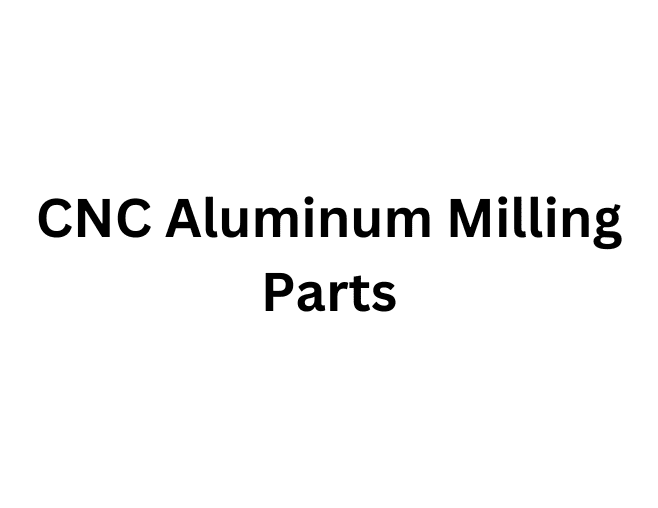
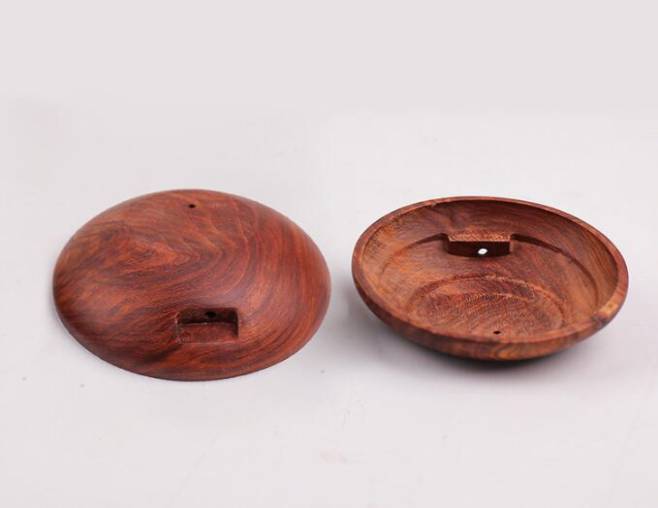
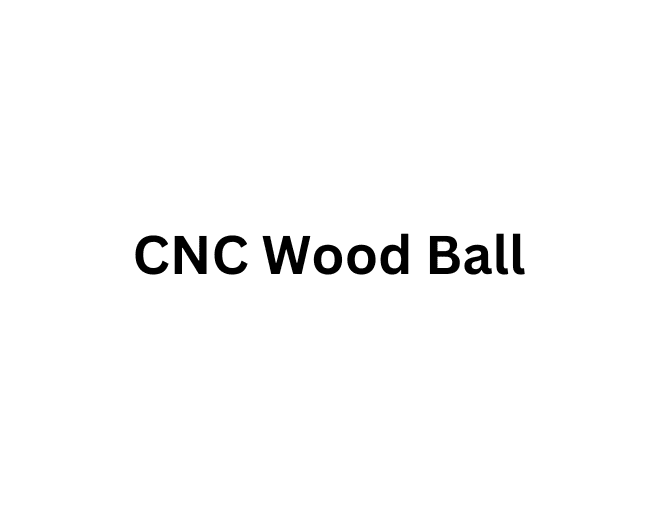
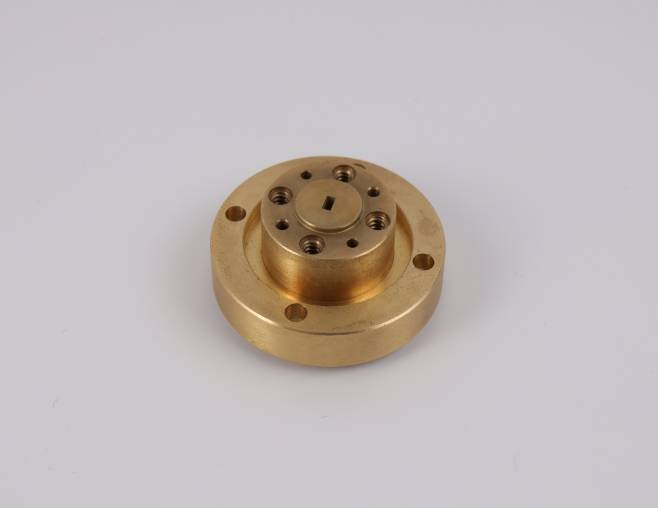
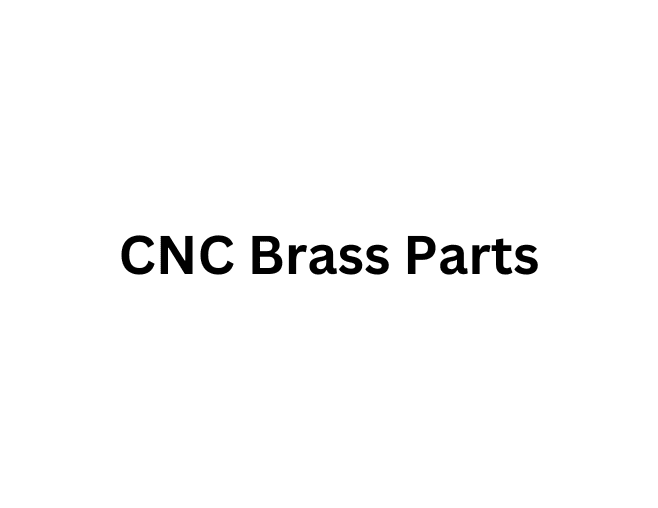

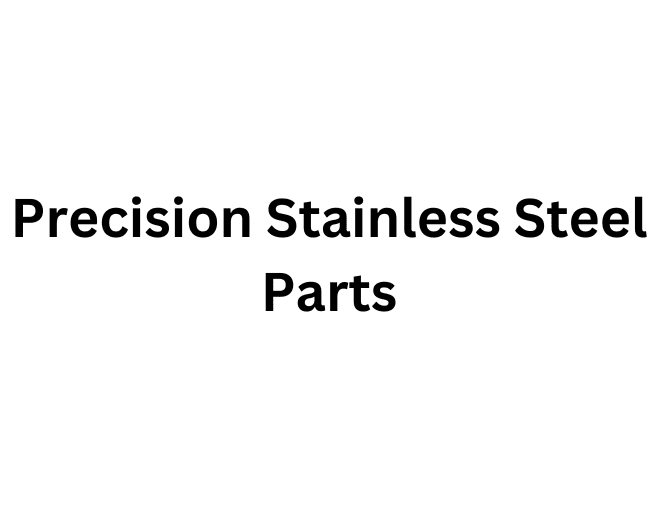
What is CNC Machining?
CNC machining is an automated process that manufactures intricate forms and geometries while retaining dimensional precision.Software that has already been programmed, and the code manages the entire production process. Little labor is needed because this process is fully automated. The traditional machining tools, which are manually operated by hand wheels or levers, are effectively replaced by this type of machine. Modern CNC machines operate more effectively because they can understand the machining language known as G and M codes.
Advantages and Challenges of CNC Machining
The industrial sector was transformed by CNC machining in the 1960s, and it is still one of the greatest machining techniques. Understanding the benefits and drawbacks of utilizing CNC machining is essential.
The following are some advantages of CNC machining :
- Maintain accuracy and precision
- Takes less time
- Flexible and compatible with different material executions
- Operator intervention is limited to the bare minimum
- High production and scalability
- Design retention
- Uniform product
Here are several challenges that arise while employing CNC machining:
- Costly with larger projects
- Always ask about size limitations when adding the order
- Annual maintenance is expensive
- It is very dependent on the training and education of the operator
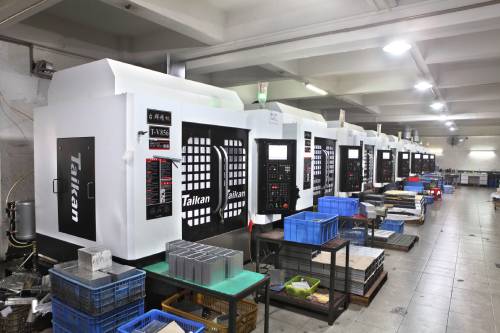
CNC Machining Process
CNC machining computerized control to operate and manipulate the machine and cutting tool to create various custom products. The steps involved in the machining process are mentioned below and are generally the same for all kinds of machining:
- Designing the CAD model
- Converting CAD files to machining language
- Setting up the CNC machine
- Running the free program to examine functionality.
- Carrying out the machining process
CNC Machining Types
CNC machining provides a range of services for producing various items. Additionally, it provides a variety of machining centers based on the type of work. Now, let's look at a few different kinds of CNC machining centers:
CNC Machining Types |
Working principle |
Working Photo |
CNC Milling Machine |
✪ Face milling
|
|
CNC Turning Machine |
The spindle is fixed in a CNC turning machine while the workpiece rotates. The cutting tools for these machines are fed in a linear motion along the revolving bar stock. It is most effective for parts with cylindrical, conical, or flat geometries. It is the key distinction between CNC mills and lathes, as CNC mills can accommodate any form |
|
CNC Swiss Machine |
✪ Milling
|
|
Surface Grinding Machine |
✪ Head and tail stocks
|
|
Centerless Grinding Machine |
✪ Machine base
|
|
Wire EDM |
✪ Widely used in mold and die manufacturing process
|
|
Deep Hole Drilling Machine |
✪ BTA (Boring and Trepanning Association) drilling
|
|
How CNC machining works?
CNC controllers collaborate with motors and drive components to move and control machine axes by executing appropriate programming. The movement of the machine is managed, automated, and controlled by a computer and CAM software using digital data. The device might be any of a wide range of CNC equipment, including a mill, lathe, router, welder, grinder, laser, water jet cutter, sheet metal, stamping machine, and many more. In the industrial sector, the cutter and speed are often continually monitored and adjusted by a sophisticated feedback system.
Size limitations for CNC machining
When acquiring or creating components with larger dimensions, it is crucial to keep these things in mind. The size of CNC machined components is restricted by machine capacity and the depth of cut necessary to achieve the specified shape.
The following factors are taken into account when evaluating the size of a CNC machine:
- Maximum machining size of machine tool
- Maximum moving distance of pallet
- Determining the maximum limit of the coordinate system
The largest milling machines can work on components as large as 3200 mm x3000mmx800mm,
These are known as gantry mills, and organizations like Boeing that manufacture substantial quantities of aluminum typically use them.And the larget turning machines is 1000mm in diameter, and the length is 1500mm.
CNC Machining Tolerances
Different sorts of tolerances must be taken into account while manufacturing items to ensure accuracy and precision. Tolerances control any machining process inherent variance.The tolerance application’s primary goal is to retain the part's functioning while allowing as many dimensions as feasible. It's crucial to remember that sometimes having tight tolerances results in more expensive machining. CNC machining requires highly well-maintained tools and equipment to achieve tight tolerance. And the part manufacturer will incur additional costs.
The tolerance chart, which is shown below, includes the following ways to examine features:
Standard Tolerance Ranges
Tolerance type | Description | Example |
---|---|---|
Standard Tolerances | Standard tolerance can be described as linear and angular measures, as well as corner chamfers and rounded parts. | +/- (0.127 mm) or .005" |
Bilateral Tolerances | The measurement of the part might differ on either side of the nominal value or actual profile in bilateral tolerance. | 30 mm (nominal value) +0.05/-0.05 mm (refers to a maximum or minimum value respectively) |
Unequally Disposed Tolerances |
It shows variation from an actual profile that is permitted in the opposite dimension unequally. | 30 mm (Actual drill hole size) Tolerance required (0.1 mm) Max and Min’s limits are like to be 30.09 or 29.99 respectively |
Unilateral Tolerances | It permits the tolerance variation from the actual value in one direction. | 30 mm (hole diameter) Tolerance required (0.2 mm) The lower limit is 30.2 mm, and the upper limit is 29.8 mm. |
Limit Tolerances | It is simply a minimum and maximum allowance dimension specified on the drawing. The key element is that this standard is used in applications where parts must fit together | 30mm (base hole diameter) The upper and lower limits are 30.0 mm and 30.1 mm |
Geometric dimensioning and tolerancing
GD&T is a system that uses symbols to describe a part's geometrical parameters. It is a tolerance-defining method that assists designers and manufacturers in controlling variations in the manufacturing process. It is crucial to remember that you will always consult the standards whenever you want to apply GD&T.
GD&T is a feature-based approach that is classified into five primary categories:
- Form controls describe the shapes of the feature, which include:
- Straightness
- Flatness
- Circularity and roundness
- Cylindricity
- Profile controls help in explaining the three-dimensional tolerance zone around the surface by using the following two features:
- Line profile
- Surface profile
- Orientation controls help in setting up dimensions that depend on the orientation of the angle. It includes:
- Angularity
- Perpendicularity
- Parallelism
- Location controls are used to define the feature’s location with the help of linear dimensioning. It may include:
- Position of feature from the datum plane or axis
- Concentricity measures the distance between the feature axis and a datum plane
- The symmetry feature helps to ensure that the non-cylindrical portion is identical throughout a datum plane.
- Runout control helps to prevent a given feature that might deviate from the axis of rotation. Two main types of runout are listed below:
- Single runout
- Total runout
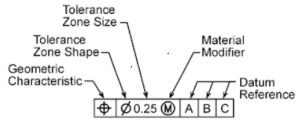
CNC Machining Materials
Many kinds of material could be used for CNC machining,you could choose the most suitable materials for your project.Worthy could handle more than 50 metal materials,
20+ plastic materials, all kinds of hardwood, softwood, enginnering woods, also composite materials.
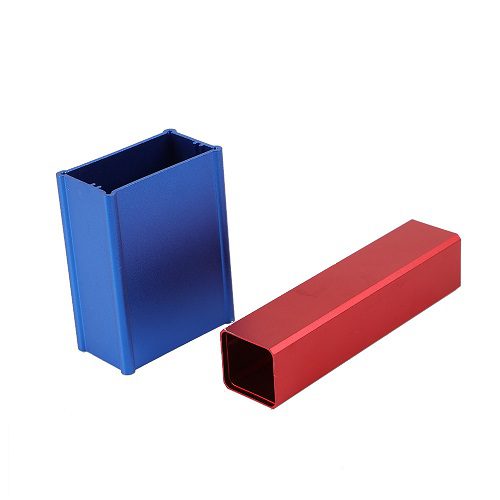
Aluminum
Grades:6061-T6,7075-T6,6060,6082,6063,5052,5083,2024,2011,2014,2017,MIC6,7050
Price:$
Tolerance:±0.05mm (±0.002″)
Finishing:Alodine,Anodizing,Paint, Powder Coating,Sand-blasting
Max part size: Milling-1200mmx1000mmx800mm, Turning-500mmx800mm
Lead time: 7-10 days
More details:
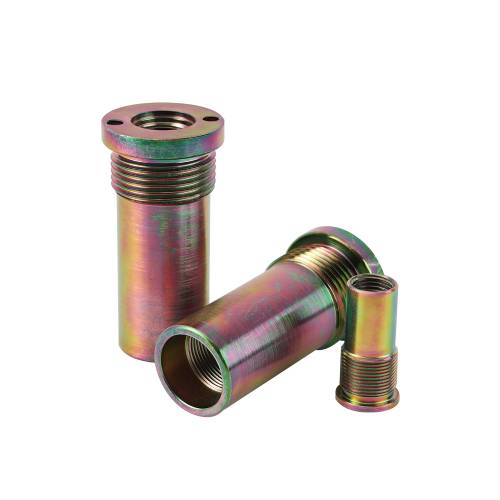
Mild Steel
Grades:12L14,1215,1018,1045,A36,S235JR,S355J2
Price:$$
Tolerance:±0.127mm (±0.005″)
Finishing:Zinc,Nickel,Paint, Powder Coating,Black oxide
Max part size: Milling-1200mmx1000mmx800mm, Turning-500mmx800mm
Lead time: 7-10 days
More details:

Alloy Steel
Grades:4140,4340,8620,42CrMo4
Price:$$$
Tolerance:±0.127mm (±0.005″)
Finishing:heat treated,zinc,nickel.
Max part size: Milling-1200mmx1000mmx800mm, Turning-500mmx800mm
Lead time: 7-20 days
More details:
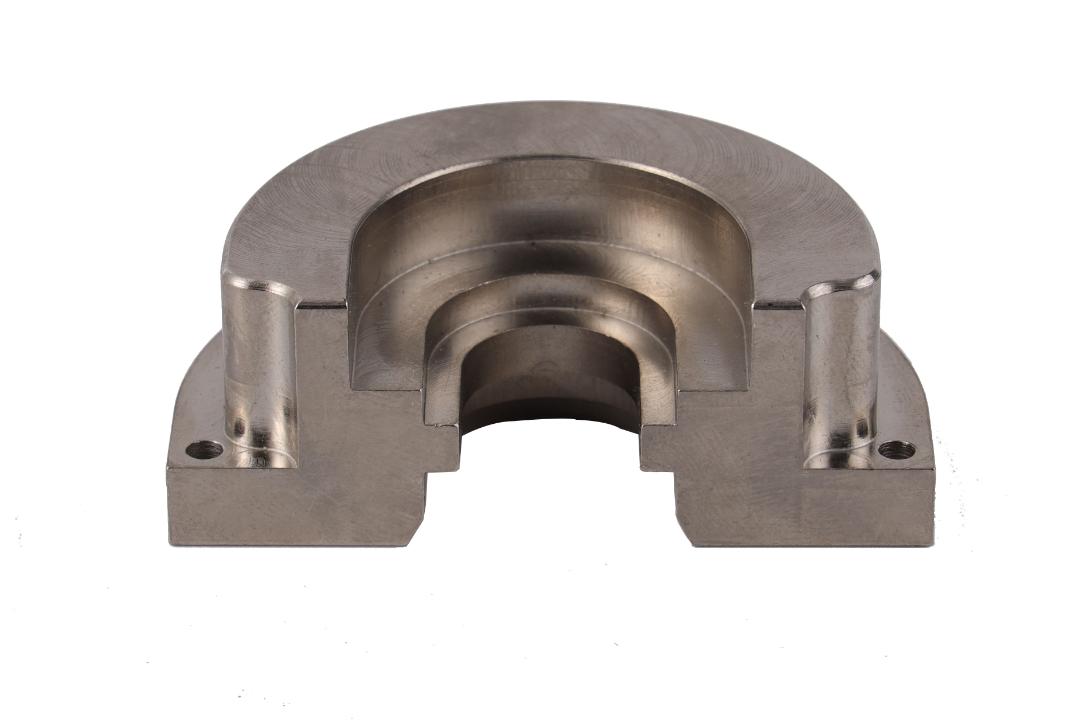
Tool Steel
Grades:D2,S7,A2,H13
Price:$$$
Tolerance:±0.127mm (±0.005″)
Finishing:heat treated
Max part size: Milling-1200mmx1000mmx800mm, Turning-500mmx800mm
Lead time: 7-20 days
More details:
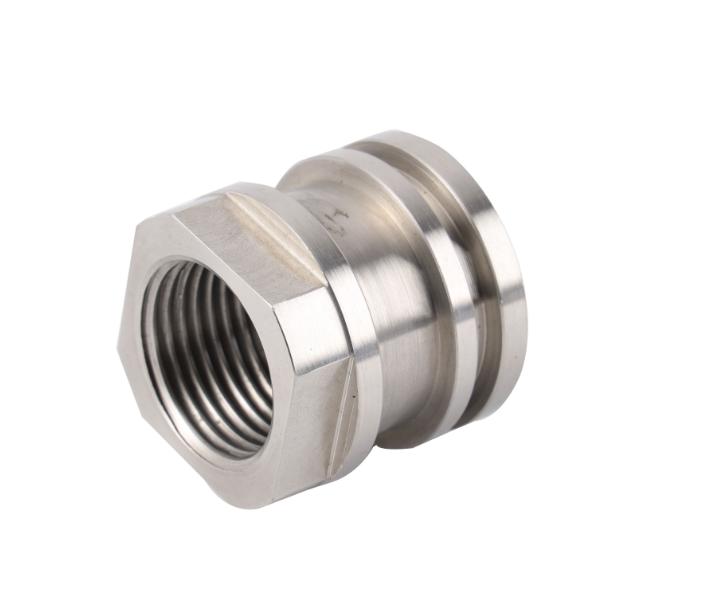
Stainless Steel
There are 4 types stainless steel: Austenitic, Ferritic, Martensitic and Duplex.
Grades:
SS201,SS301,SS303,SS304,SS316,SS316Ti;
SS409,SS433,SS434,SS444;
SS410,SS420,SS430,SS440,17-4PH;
SS2205,SS2304
Price:$$$$
Tolerance:±0.127mm (±0.005″)
Finishing:Polish,chrome,black oxided,passivation
Max part size: Milling-1200mmx1000mmx800mm, Turning-500mmx800mm
Lead time: 7-15 days
More details:
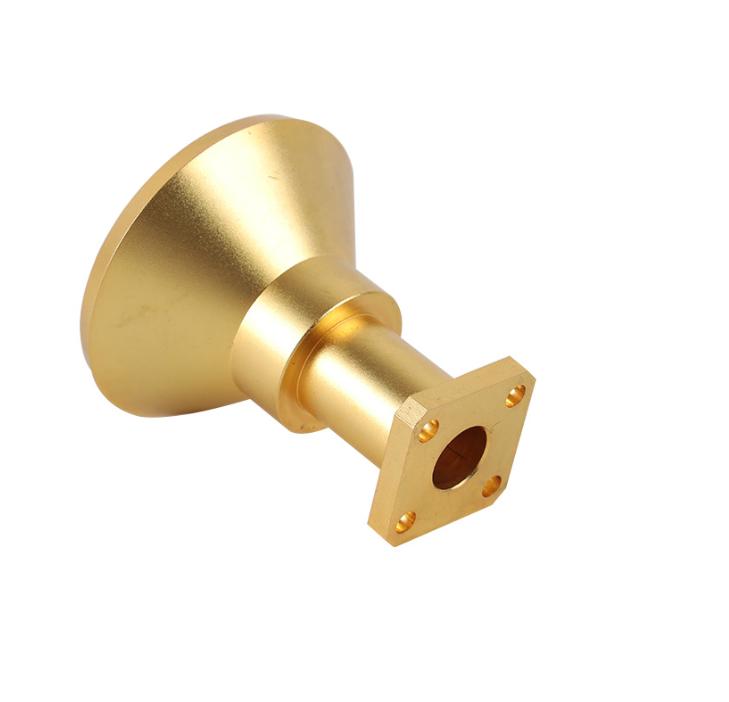
Brass
Grades: C360 ,C260, C385
Price:$$$
Tolerance:±0.127mm (±0.005″)
Finishing:Nickel,Gold plating.
Max part size: Milling-1200mmx1000mmx800mm, Turning-500mmx800mm
Lead time: 7-10 days
More details:
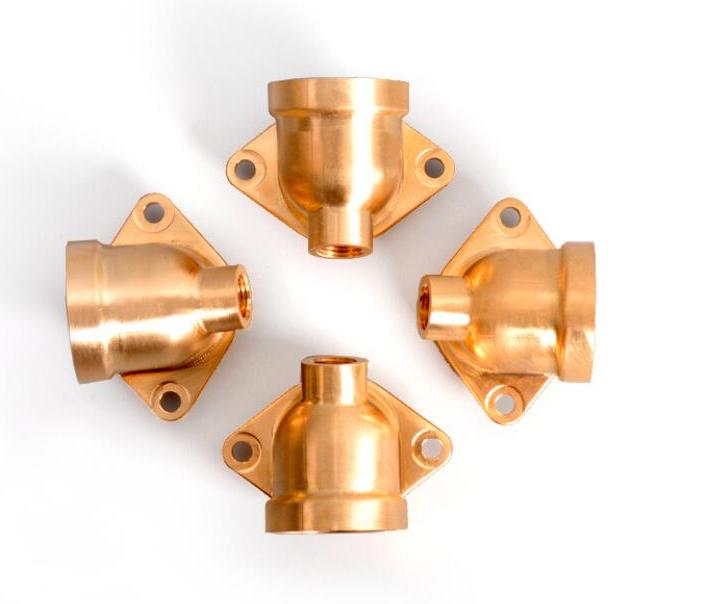
Copper
Grades: C110,C101
Price:$$$$
Tolerance:±0.127mm (±0.005″)
Finishing:Polished,Gold plating.
Max part size: Milling-1200mmx1000mmx800mm, Turning-500mmx800mm
Lead time: 7-10 days
More details:
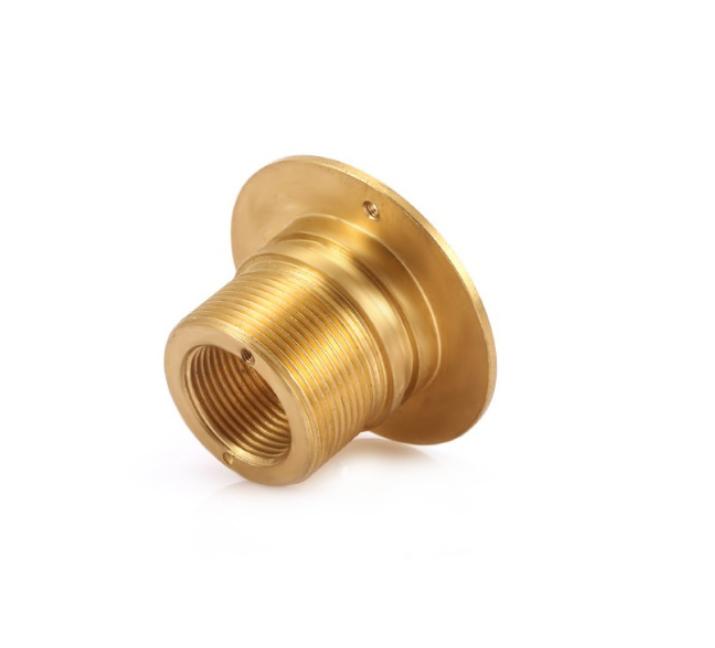
Bronze
Grades: C93200 and C59400
Price:$$$$
Tolerance:±0.127mm (±0.005″)
Finishing:Polished,Gold plating.
Max part size: Milling-1200mmx1000mmx800mm, Turning-500mmx800mm
Lead time: 7-10 days
More details:
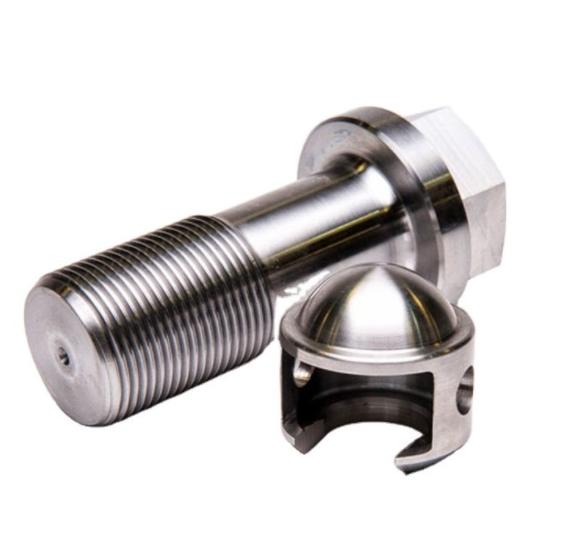
Titanium
Grades: Grad 5 and Grade 2
Price:$$$$$
Tolerance:±0.127mm (±0.005″)
Finishing:Sand blasting,Polishing,anodizing
Max part size: Milling-1200mmx1000mmx800mm, Turning-500mmx800mm
Lead time: 7-10 days
More details:
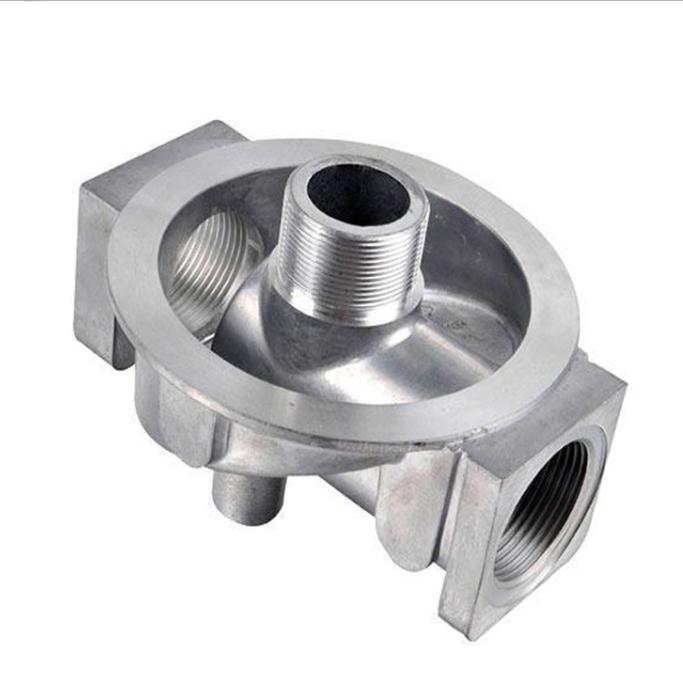
Magnesium
Grades: AZ91D, AZ61B, and AZ31
Price:$$$$
Tolerance:±0.127mm (±0.005″)
Finishing:Anodizing, powder coating
Max part size: Milling-1200mmx1000mmx800mm, Turning-500mmx800mm
Lead time: 7-10 days
More details:
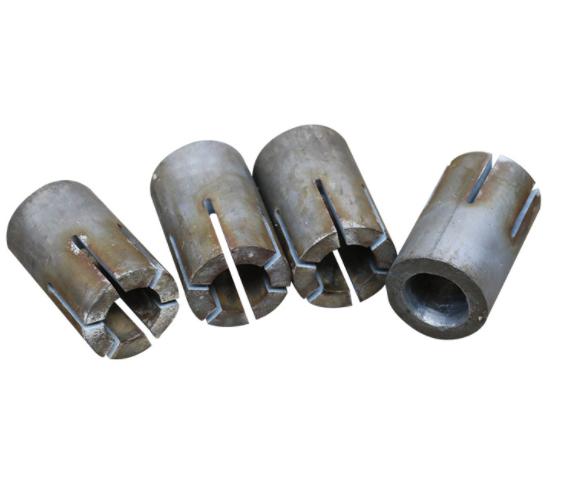
Lead
Grades: Lead alloy
Price:$$$$
Tolerance:±0.127mm (±0.005″)
Finishing: powder coating
Max part size: Milling-1200mmx1000mmx800mm
Lead time: 7-10 days
More details:
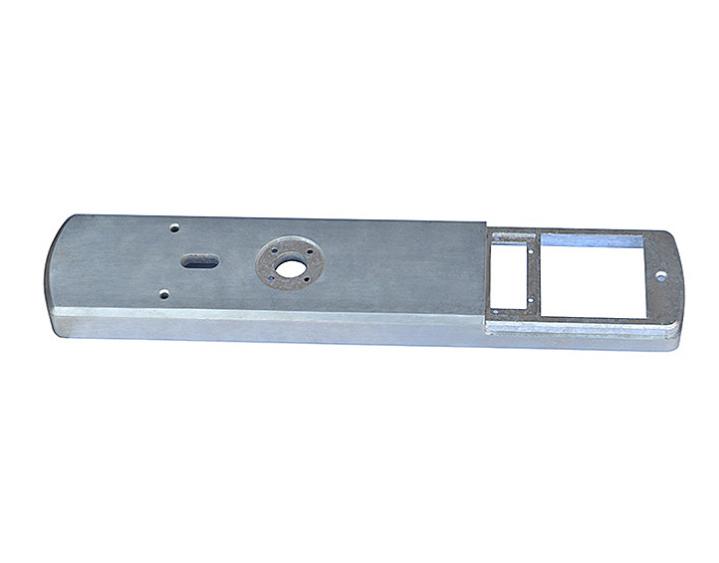
Zinc
Grades:Zinc alloy
Price:$$$
Tolerance:±0.127mm (±0.005″)
Finishing: powder coating
Max part size: Milling-1200mmx1000mmx800mm, Turning-500mmx800mm
Lead time: 7-10 days
More details:
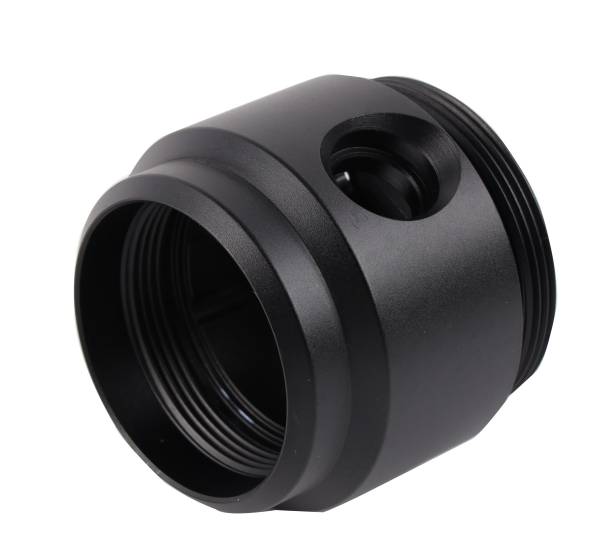
POM (Delrin/Acetal)
Color:White,black
Max part size: Milling-1200mmx1000mmx800mm, Turning-500mmx800mm
Lead time: 5 days
More details:
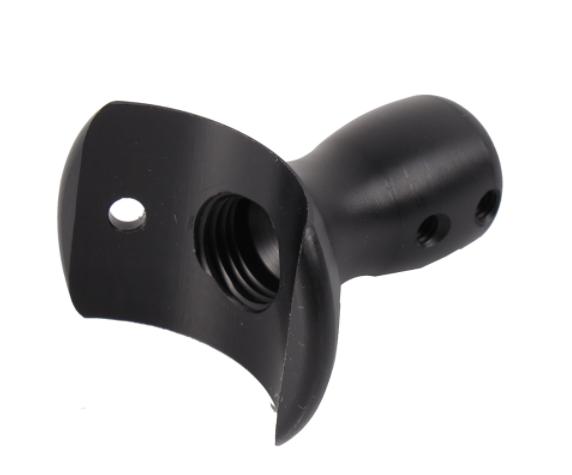
Nylon (Delrin/Acetal)
Grades:PA6
Color:White,black
Lead time: 5 days
More details:
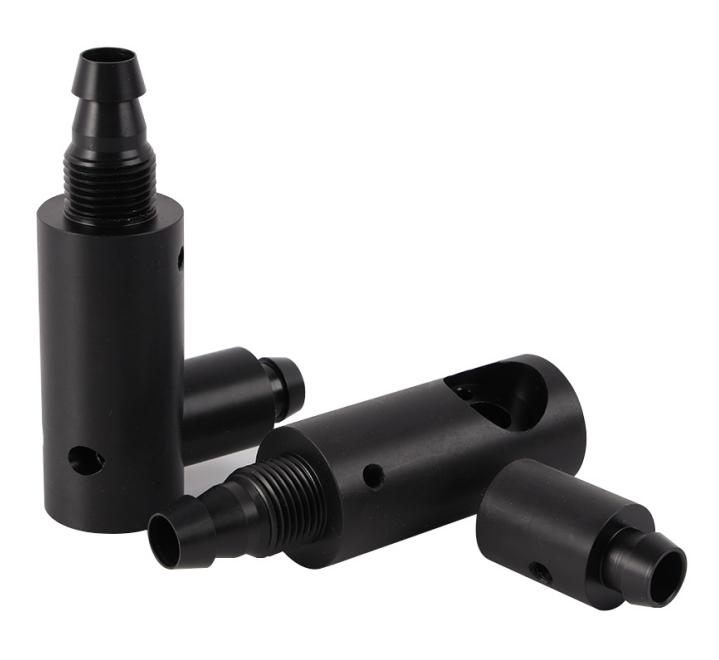
ABS
Color:White
Lead time: 5 days
More details:
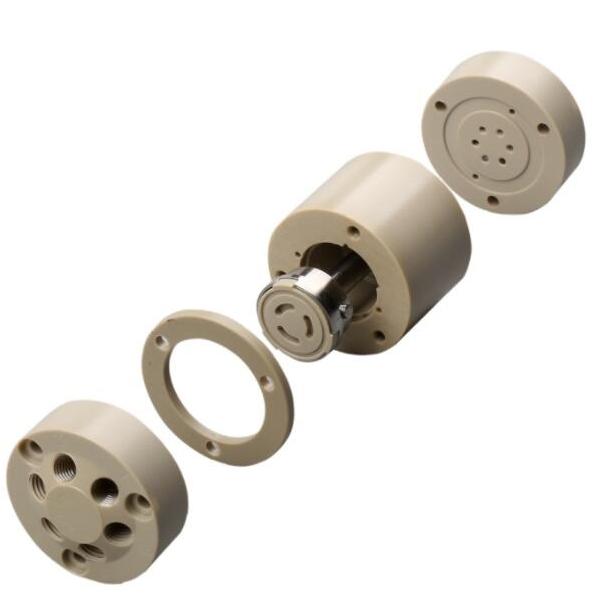
PEEK
Color:Brown, black
Lead time: 5 days
More details:
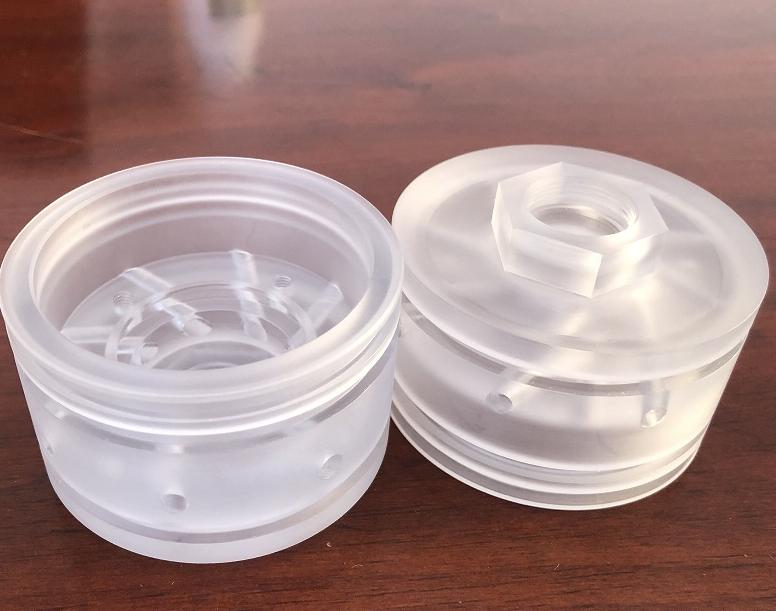
Polycarbnate (PC)
Color:Transparent
Lead time: 5 days
More details:
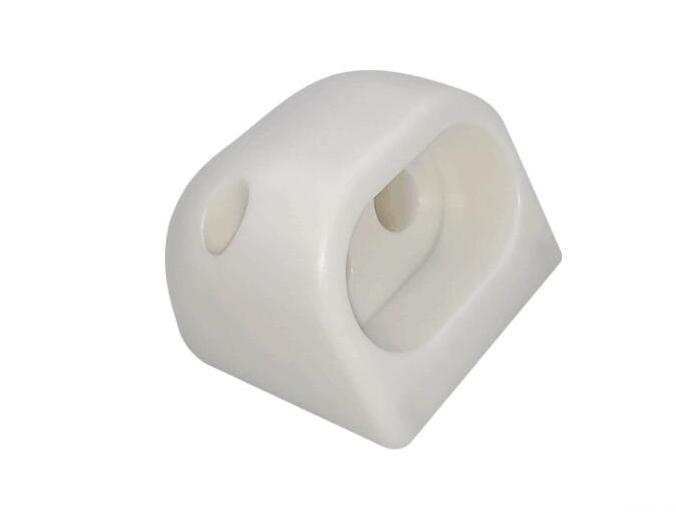
Polyethylene (PE)
Color:White
Lead time: 5 days
More details:
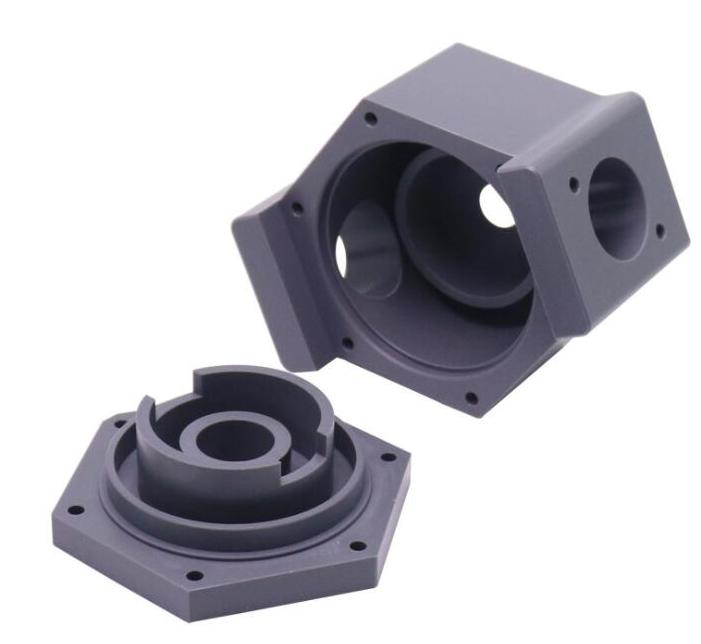
PVC
Color:White,Grey
Lead time: 5 days
More details:
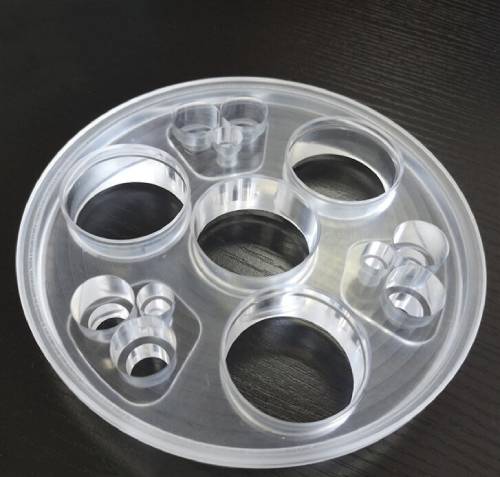
PPMA
Color:Transparent,black
Lead time: 5 days
More details:
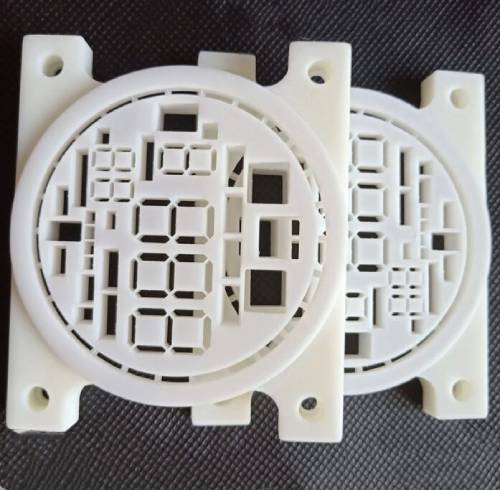
PTFE (Teflon/F4)
Color:White,black
Lead time: 5 days
More details:
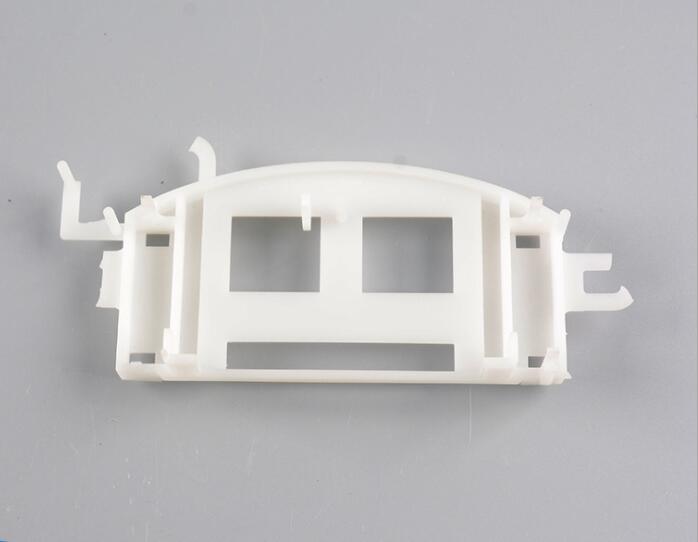
Polypropylene (PP)
Color:White
Lead time: 5 days
More details:
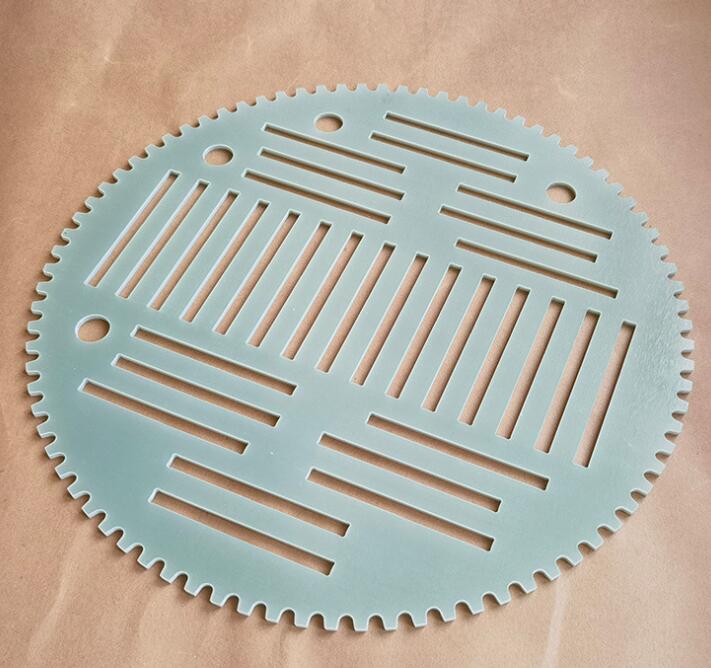
Garolite G10
Color:Brown,yellow, green
Lead time: 5 days
More details:
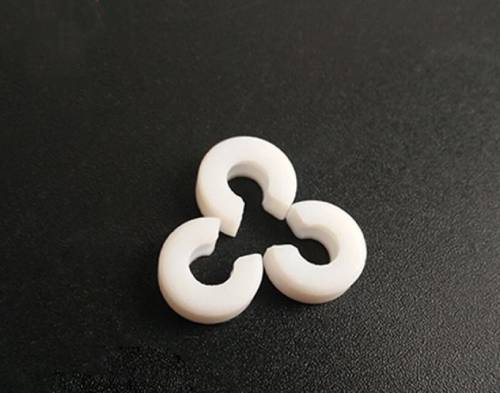
PET
Color:White,Yellow
Lead time: 5 days
More details:
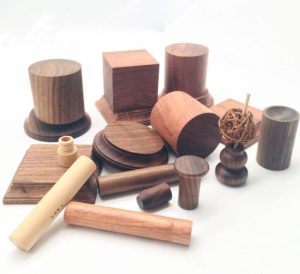
Hardwood brands:Black Walnut, Beech, Oak.Maple, Cherry, Mahogany, Birch, Ash, Poplar, Rosewood, Teak
Softwood brands: Pine,Fir,Redwood,Cedar,Spruce
Enginnering wood brands: Bamboo,MDF
More details:
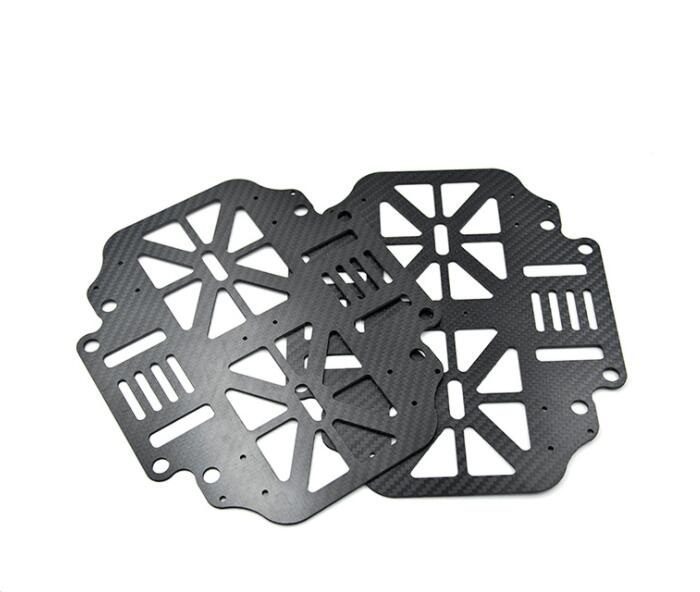
CNC Machining Finish
In the process of CNC machining, there will inevitably be tool marks.If you are looking for a high quality surface,we could support 30+ surface finish.However we are not limited to these,if below listed finish could not match your requirements, please help to send them for quote. Because the surface finish will affect the part dimension, we do not recommend applying secondary finishes to high-tolerance parts, as the surface finish can remove or add enough material to put the finished part out of size tolerance.
Showcase | Surface Finish | Description | Applicable Materials | Color | Pros and Cons |
---|---|---|---|---|---|
![]() |
As machined Ra3.2μm | The standard as machined surface roughness is 3.2 μm (125 μin),so there is tool marks and burrs left on the surface. | Metal,plastic,wood | None | Pros: Tightest dimensional tolerances;No added cost (for standard finish) Cons: Visible tool marks |
![]() |
Smooth machining Ra1.6μm | The standard as machined surface roughness is 1.6 μm (64 μin), Machine marks are less evident but still visible. | Metal,plastic | None | Pros: Tightest dimensional tolerances;No added cost (for standard finish) Cons: Less visible tool marks |
![]() |
Fine machining Ra0.8um | Fine machining could ensure the dimensional tolerance, line tolerance and surface roughness of the product. The standard surface roughness is 0.8 μm (32 μin) | Metal | None | Pros: Tightest dimensional tolerances No visible tool marks Cons: Add additional cost |
![]() |
Polishing Ra0.4μm | Polishing is a processing that uses mechanical, chemical or electrochemical method to reduce the surface roughness of the parts.The standard surface roughness is 0.4 μm (12 μin) | Metal | None | Pros: Tightest dimensional tolerances No visible tool marks Cons: Add additional cost |
![]() |
Anodize Type II | Anodizing is an electrochemical process that converts the metal surface into a decorative, durable, corrosion-resistant, anodic oxide finish | Aluminum | Any Color | Pros: Durable, cosmetic coating. Cons: Compatible only with aluminum and titanium alloys. |
![]() |
Hard Anodize Type III | The anodizing file for hard anodize is between 25 to 150um, which could improve various properties of aluminum,such as corrosion resistance, wear resistance. | Aluminum | Clear, Black,Red | Pros: superb abrasion and wear resistance, and excellent dielectric properties. Cons: Limited color selection;will affect the specified area dimension. |
![]() |
Alodine | Alodine is a chromate conversion coating that protects aluminum from corrosion. | Aluminum | Clear, Gold | Pros: ability to self-heal small imperfections, rubs or scratches;low cost. Cons: compared with anodizing,low corrosion resistance, appearance is not uniform. |
![]() |
Sand-Blasting | Sandblasting is a process that uses the impact of a high-speed sand stream to clean and roughen the surface of a substrate. | Metal,plastic | None | Pros: Uniform matte or satin finish and Low-cost surface finish No visible tool marks Cons: Affects critical dimensions and surface roughness |
![]() |
Brushing | Brushing is mainly through the mechanical relative movement of abrasive materials on the metal surface and chemical corrosion in the metal surface to get a layer of macroscopic rough straight surface with uniform distribution of coarse and fine. | Metal | None | Pros: Eliminate slags and other defects that occur due to welding and other processes. Cons: Cleaning of brushed surfaces may be difficult;May cause damage to surfaces. |
![]() |
Chrome Plating | Chrome plating is the act of plating chromium as a coating onto other metals | Aluminum, Steel, Stainless Steel, Brass, Bronze, Copper | Bright,Black | Pros: increase the surface hardness of the plated parts;could protect the surface from rust Cons: the plating process can result in poor adhesion due to micro-cracks or poor surface preparation;the price for chrome plating is very expensive. |
![]() |
Passivation | Passivate is a widely-used metal finishing process to prevent corrosion | Stainless steel, Brass, Bronze, Copper | --- | Pros: better corrosion resistence,uniform and smooth finish/appearance and shiny surface. Cons: does not smooth out the surface of the metal;requires a pre-cleaning operation,hich will extend the time required to complete the process |
![]() |
Phosphate Plated | It is a chemical and electrochemical reaction to form a phosphate chemical conversion film. | Steel | Black | Pros:could protect the surface from rust Cons: it has some ill effects on nature and surroundings. |
![]() |
Electrophoresis Coating (E-coating) | Electrophoresis coating is a painting process that parts are immersed in a paint solution contained in an electrified tank.The paint ions gain or lose electrons at the surface of the part and are changed to solid paint that attaches to the surface. | Stainless Steel,Steel.Aluminum | Black | Pros:uniform coating; High production efficiency Cons:Can not increase the coating thickness; Only for metal substrate. |
![]() |
Carburizing (Case Hardening) | Steel parts are heated and held in carburizing medium, so that carbon atoms penetrate into the surface of the steel parts and the carbon concentration on the surface is changed | Steel | Black | Pros: increases wear resistance and corrosion resistance; Cons:Increased machining costs |
![]() |
PTFE coating | PTFE coating is non-stick, fluoropolymer, high temp coatings. | Metal, glass | Black | Prons:It is non-adhesive,wear resistance and corrosion resistance; Cons: high cost ,unweldable |
![]() |
Varnish surface finish | Varnish is a transparent, hard and protective finish which generically used in wooden products to give it a glossy finish while forming a protective film around it | Wood | Transparent | Pros: a very real protective shield that makes the wood waterproof and highly resistant to wear and tear. Cons: Clear and bad scent;Turns yellow in time |
![]() |
Lacquer surface finish | Lacquer is a type of quick-drying, solvent-based finish which has been often used on wooden objects | Wood | Black ,White | Pros: extremely intense gloss finish; durable and resistant to damage Cons: begin to discolor and become scratched as time goes by. |
![]() |
Zinc Plate | Zinc plating is a surface treatment technique that applies a layer of zinc to the surface of metals. | Steel | Black,White,Yellow,Bule | Pros: Cost-Effective;Attractive Finishing Touch;Ductility and Durability Cons: distributing the coating evenly over the metal’s surface can be challenging;zinc usually does not perform fine at high temperatures. |
![]() |
Nickel Electroplating | Nickel electroplating is the process of applying a nickel coating onto a metal surface by means of electrolytic deposition. | Metal,Ceramics | Bright, Black | Pros: the surface is smooth and birght, and could strong bonding with ceramic and metal layer. Cons: easy to have the spots on the surface. |
![]() |
Nickel Electroless plating | Nickel Electroless Plating is a process that deposits an alloy of 90% nickel and 10% phosphorus on a wide range of metals | Aluminum, Steel, Stainless Steel | Bright | Pros: It provides additional wear- and corrosion resistance surface. Cons: expensive ;To ensure effectiveness, the plating process requires consistent monitoring. |
![]() |
Power Coating | Powder is the use of corona discharge phenomenon to make the powder coating adsorbed on the workpiece. | Aluminum, Steel, Stainless Steel | Black ,White | Pros: high working efficiency;cover the surface defects; Cons: the surface coating is not uniform; easy to pollute the environment |
![]() |
Tin plating | Tin plating is a process where a thin layer of silver is applied to metals. | Metals | gray-white | Pros:Good solderability,Corrosion resistance and good resistance to adhesive wear. Cons:High strength steel is sensitive to hydrogen embrittlement |
![]() |
Black Oxided | Black oxided is a common means of chemical surface treatment, the principle is to produce a layer of oxide film on the metal surface to isolate the air and achieve the purpose of rust prevention. | Steel, Stainless Steel | Black | Pros: cheaper,decorative finish,dose not significantly change the dimensions of the fasteners as hot dip galvanizing does. Cons: The black oxide finish can be easily rubbed off,then they will be rust in the right environments |
![]() |
Electropolishing | Electropolishing is an electrochemical finishing process that removes a thin layer of material from a metal part. | Metal | --- | Pros: could improve the surface roughness;High production efficiency. Cons:impossible to remove surface defects such as deep scratches. |
![]() |
PVD Vacuum Plating | PVD is an industrial manufacturing process, i.e., vacuum coating, that gives products a beautiful metallic texture and excellent performance. | Metal,Plastic | Rose, Gold | Pros:improve the surface's strength and durability;More environmentally friendly. Cons:higher costs |
![]() |
Gold plating | Gold plating is a process where a thin layer of gold is applied to metals. | Metals | Gold | Pros:improve the surface's hardness Cons:higher costs |
CNC Machining Design Guidelines
The following are some crucial guidelines to be considered to minimize operating, machining, and procurement costs:
- Design the part with rounded corners, whether internal or external.
- Avoid deep pockets as much as possible.
- Use standard drill size
- Take Material Rationality into account.
- Avoid thin walls and optimize the length of threads.
- Try to mention tight tolerance if necessary; otherwise, avoid mentioning it.
- Avoid intricate features with a high aspect ratio.
- Make effective use of surface finish in microns. The cost will significantly increase if you add a surface finish to non-functional sections.
From CNC Prototyping to Production
Computerized numerical control (CNC) machining is a subtractive method that produces the required form or geometry by rotating various cutters at high speed.Worthy could supply the below custom CNC service.
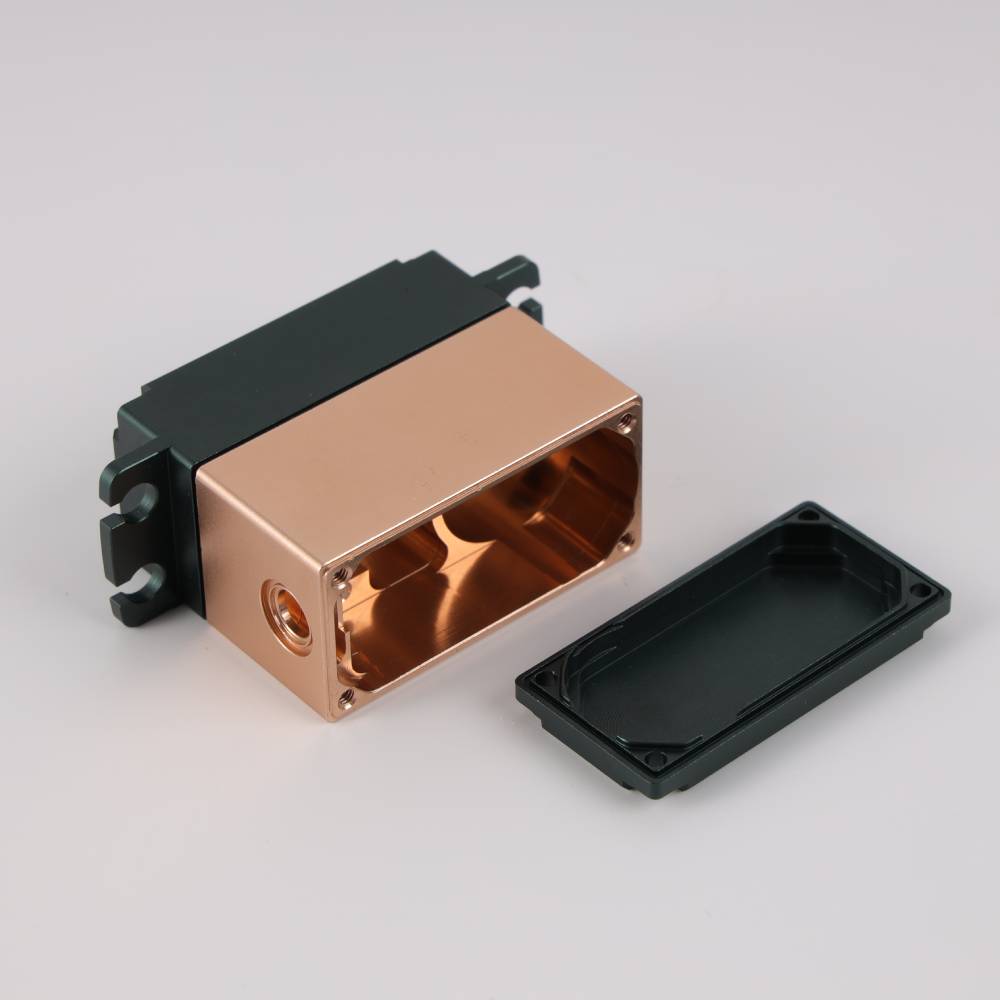
Rapid Prototyping
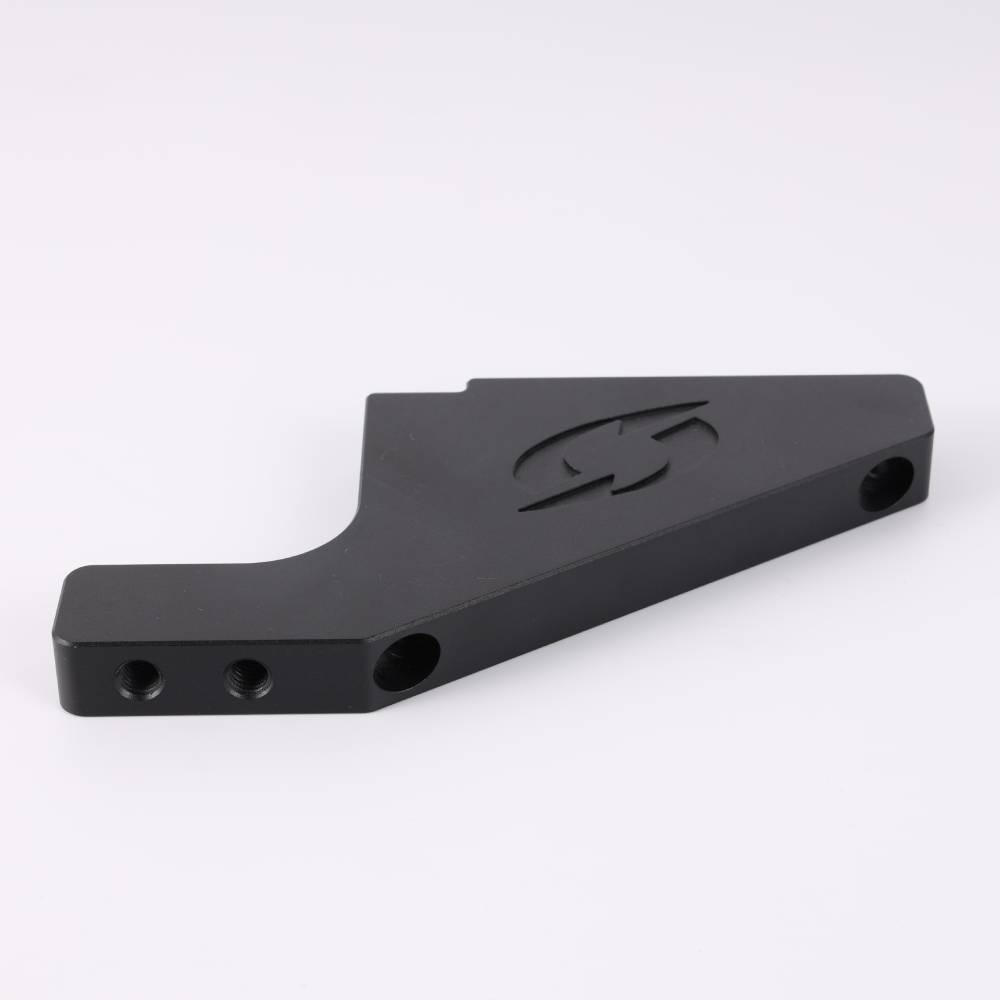
Production
Worthy Hardware Advantages
When you source the CNC Machining shops from the world, there are huge numbers of CNC machining service providers. Why you should choose Worthy Hardware as your trust vendor?
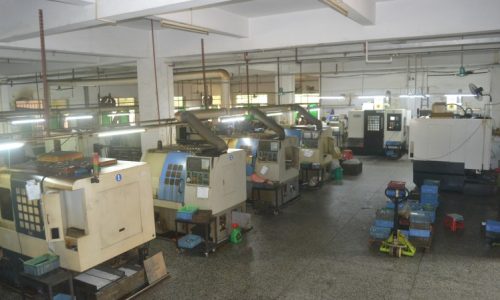
Advantage 1: Comprehensive Capabilities
As the leading manufacturer of CNC machining for over 25 years, we are well equipped with 35 sets CNC Machines, including 3 sets 5 axis ,4 sets 3 axis, 12 sets turning and milling compound. These machines could allow us to make prototypes, small batch and mass production parts. The fastest delivery time is 3 working days.
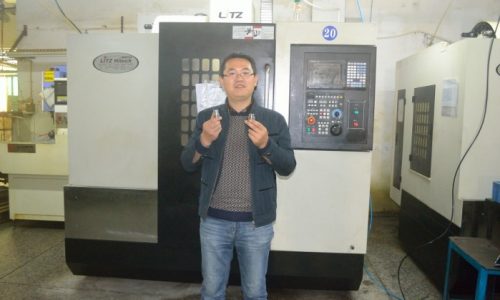
Advantage 2: Rich Experience
As the leading manufacturer of CNC machining for over 25 years, we are well equipped with 35 sets CNC Machines, including 3 sets 5 axis ,4 sets 3 axis, 12 sets turning and milling compound. These machines could allow us to make prototypes, small batch and mass production parts. The fastest delivery time is 3 working days.
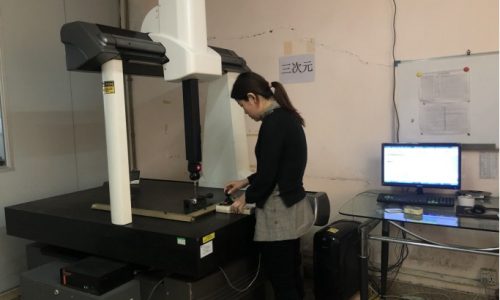
Advantage 3: Strict Quality
As the ISO 9001:2015, certified quality management system, all the team, material and machines are in regular status of quality assurance, we make it correct at the first time not only to ourselves, but also to our customers. We check and maintenance the machines everyday except the holiday time. In the production stage including the samples, the production workers check the dimensions frequently, and then the production manager will check the dimension again, finally our QC department will make the final checking with CMM. We make the 100% inspection for the parts, especially for the thread and surface.
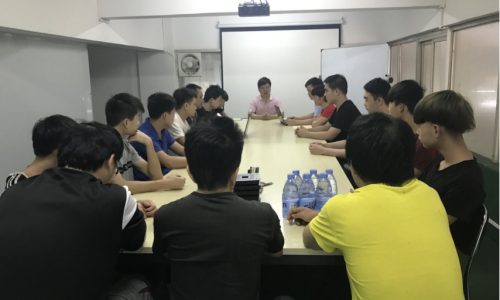
Advantage 4: Stable Employees
80% of the workers in Worthy Hardware have worked here for more than 12 years , and most are home fellows. They’re settled down in Donguan already. Therefore, we can be assured that quality and delivery time will not fall apart anytime soon because we’ve already been through all these hardships together as one family!
Customer Testimonials
In the past 25 years, our clients are all over the world, including the world's top 500 companies such as Jabil, ABB, Medtronic and so on.
Do you want to know what our customers say about us? Let's take a look.
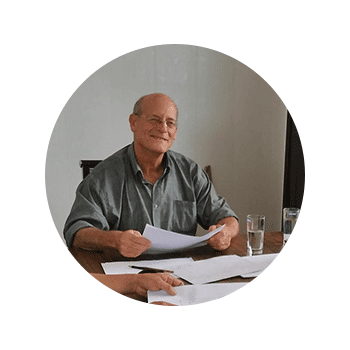
Justin, CEO of a lighting company
With most factories, I have a moment of fear before I open their boxes. Will the components be made correctly? Do they care about quality? It is often a war. And Dennis has to fight the war, treating most factories like small children!
But, not your company. You’re company is world-class. You make beautiful components! Thank you very much for your hard work. We will work together for many lifetimes!
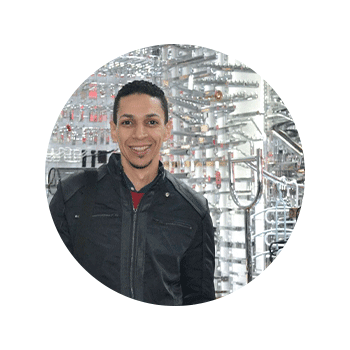
David, General manager for a family owned business
CNC Machining FAQ
For a fraction of the price of traditional CNC machining, manufacturers who make the conversion may use 3D printing technology to create and fabricate components in a single day. But there are still a few key areas where CNC could be an excellent opportunity to manufacture parts.
Following are a few distinctions between CNC and 3D printing, as well as their purposes and physical features:
CNC Machining | 3D Printing |
---|---|
The smallest element that can be manufactured with CNC depends on the tool length and diameter. | In 3D printing, the nozzle diameter determines the manufacturing volume. |
By choosing the appropriate tool, CNC may manufacture a product with smoother surfaces than 3D printers. | High smoothness and manufacturing capabilities are also offered by 3D printing but at a considerably higher cost than CNC. |
Use CNC machining if the product is urgently required and there can be no delays in the process. | However, if the piece’ requirement can be retained until the machine is free; in this situation, 3D printing can provide the part, depending on its size and deposition rate. |
There might not be a clear-cut choice between CNC machining and injection molding when it comes to production techniques. The production team must evaluate each process’s benefits and drawbacks concerning the overall project's budget, design, and technical requirements before deciding on the optimum manufacturing approach.
Key differences between CNC machining and Injection molding include the following:
CNC Machining | Injection molding |
---|---|
Computerized numerical control (CNC) machining is a subtractive method that produces the required form or geometry by rotating various cutters at high speed. | The injection molding technique involves heating thermoplastic resin pellets, and molten material is poured into a hardened steel mold through a pressurized nozzle. |
In the case of large volume, CNC machining is significantly more expensive than injection molding per unit. | Injection molding is often the one that is financially viable when big-scale or large-volume manufacturing is necessary. |
CNC machining tools may cut material by maintaining the accuracy of 0.001". | Injection molding tools are normally set to standard tolerances of 0.005" and tend to have tolerance coarser than CNC. |
CNC machining of the parts may often be more effective with tight tolerance than IM. | Injection molding is costly because of the high cost of manufacturing molds with extremely tight accuracy. |
What are your maximum dimensions for CNC machining?
Every CNC machine shop will have a constraint on the component size. Coordination with your manufacturing partner is necessary, and you should aim to design parts with their machining capacities. The following are our dimensional boundaries:
Our CNC Milling-1200mmx1000mmx800mm (47.24”x37.37”x31.49”)
Our CNC Turning-500mm in diameter x800mm in length (19.68”x31.49”)
What’s your CNC machining capacity?
Machine-hour capacity is another name for the daily total production capacity. The daily total output capacity is easily determined. i.e., it can continue to operate for 24 hours each day because we have more than 35 sets CNC machines.And one day we could manufacture 5000pcs parts.
How much does your CNC machining service cost?
The cost of a CNC machining service is determined by the type of product being manufactured or designed. The machining services cost varies according to your design intricacy. The following elements are taken into account when calculating the overall production cost:
- The specific cost of your order
- Material cost
- Shipping cost
- Machining cost
- Labor cost per hour
- Additional services cost
For Worthy, our machining cost per hour is 12.7$-15.87$.
What is your tightest tolerance?
Every component's tolerance depends significantly on its nature and specifications. Holding tight tolerance is a major element we consider when providing machining services. As technology advances, there is more competition in the market. However, as our customer, we give you control over pricing vs level of intricacy. Sometimes we could hold 0.001mm tolearnce.
How you could guarantee the quality?
The machine or tool you utilize throughout the production process will determine the quality of a CNC machined component. Many different types of CNC machines are available and commonly categorized as 3-axis, 4-axis, and 5-axis CNC machines.
It is to be noted that just the availability of top-notch machinery is not enough. Proficient human resource ensures that the quality does not deteriorate by using appropriate tooling with multi-axis machines.
CNC Machining Applications
Many manufacturing industries, including automotive, aerospace, construction, and agricultural, use CNC machining as a manufacturing technology. It is also appropriate for various engineered materials, including wood, brass, stainless steel, alloy steel, PEEK, PTFE, and many other composite materials.
Following are some examples of applications where CNC may offer its services more effectively:
For product developers that want high-quality parts in small quantities to be used as prototypes, testing samples, or as a stepping stone to full-time manufacturing, CNC machining may be the ideal alternative. The following services may benefit rapid prototyping:
- CNC machining is fast
- No fixed tooling
- Provides accuracy and precision
- Easy to modify
- Able to work with various material executions
When producing complicated items in small quantities, CNC machining may be helpful. It may also have various tools for research and development projects, including gauges, jigs, fixtures, and other tools. Additionally, it could support clients who are more likely to need short-run production.
Rapid tooling is most comparable to quick prototyping since it uses a procedure that a CNC machine would most likely employ for rapid prototyping. It is a highly developed and successful process that aids in producing multiple pieces by the design. We might also state that rapid tooling is about efficiently achieving accurate results.
Due to its automation and ability to quickly produce goods in large quantities, CNC machining is the most excellent option for mass production. Because of its automated capability, the finished product has fewer flaws, such as scratches or blemishes. It executes many activities simultaneously, resulting in increased productivity and efficiency.
Getting the desired and exact manufactured product is something that every client and manufacturer wants. Every component in the aviation industry is crucial and demands high precision and accuracy. As a result, CNC machining is among the most remarkable production techniques for generating a variety of aerospace parts. A few of the critical features produced with CNC machining are listed below:
- Shafts
- Oxygen generation components
- Valve components
- Electrical connectors
- Housing
- Filter bodies
The usage of CNC machines in the automotive industry has also advanced significantly. It may be used in the industry’s prototype and manufacturing processes as well as in the creation of automotive components. CNC technology has increased output levels in the automobile sector by accelerating the manufacturing process. The following is a list of the components of automotive that CNC machining may produce:
- Cylinder heads
- Drive axles
- Gearboxes
- Starter motor
CNC machining is employed in many fields nowadays, not only in the industrial sector. When it comes to the medical field, it is utilized to produce a variety of medical equipment that may be used for a wide range of different items, such as artificial joints, dental work, and several surgical equipment. By assuring great accuracy, it is an intelligent approach to save costs and improve repeatability in the medical profession.
The effectiveness and precision of CNC technology are well acknowledged. Defense industry suppliers seek methods to reduce costs and lead times without jeopardizing quality and safety. The following are some examples of military components manufactured using CNC technology:
- Radome and radar dish systems
- Tomahawk missiles
- Riffle nozzles and many more
In today's world, the energy industry is the central segment. Hydraulic valves for the oil and gas sector, solar cells, and wind turbine parts are just a few examples of cutting-edge machinery needed for diligent energy generation. CNC machining is essential for producing intricate patterns and geometries.
The most widely used method of machining in the electrical sector is CNC because CNC machining maintains a high degree of precision and is an automated process. The following are a few examples of electronic components made using CNC machining:
- Microchips
- Circuit boards
- Sensors and transistors
- Heat sinks