What Materials Used in Precision Machining for Automotive Parts?
Alloy Steels
Alloy steels are favored in automotive machining for their strength and durability. Enhanced with elements like chromium, nickel, and molybdenum, these steels withstand extreme pressures and temperatures, making them ideal for engine parts and transmissions.
Stainless Steel
Stainless steel is renowned for its corrosion resistance and strength, making it a top choice for automotive parts that must endure harsh environments. It’s particularly used in exhaust systems and decorative trims.
Aluminum
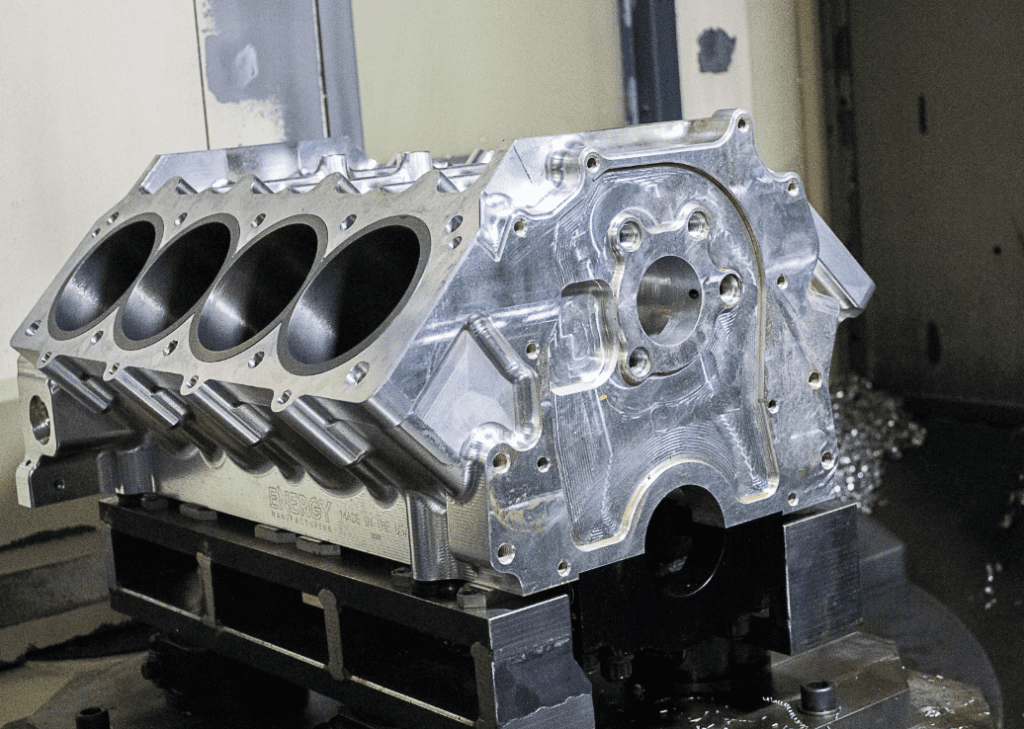
Aluminum stands out in automotive machining for its lightweight nature, which helps in enhancing fuel efficiency and reducing emissions. It’s commonly used in engine blocks, transmissions, and chassis components.
Precision Steel
Precision steel is crafted to meet strict tolerances and high-quality standards, essential for critical automotive components such as gears and bearings, where exact dimensions are crucial for optimal performance.
Brass
Brass is utilized in automotive machining for components that require low friction and excellent corrosion resistance, such as fittings and connectors within the fueling and cooling systems.
Titanium
Titanium is prized for its exceptional strength-to-weight ratio and corrosion resistance. It’s typically used in high-performance automotive applications like racing cars for components like connecting rods and valve train systems.
Copper
Copper is essential in automotive machining for its excellent conductivity, making it ideal for electrical components, wiring, and cooling systems where heat transfer is critical.
Special Alloys
Special alloys in automotive machining are designed to meet specific needs such as high heat resistance or unique strength requirements. These materials are used in components that face extreme conditions, ensuring reliability and longevity.
PVC
PVC (Polyvinyl Chloride) is used in automotive machining for its flexibility, durability, and resistance to environmental factors. It is typically employed in vehicle interiors and cable insulation, offering both functionality and cost-effectiveness.
UHMV
UHMV (Ultra High Molecular Weight Polyethylene) is known for its extremely high abrasion resistance and impact strength. In the automotive industry, it’s used for wear-resistant components, such as guide rails and protective pads.
Nylon
Nylon is a versatile material favored for its strength, temperature resilience, and wear resistance. It’s commonly used in under-the-hood applications, such as in bushings, bearings, and other moving parts where lubrication is minimal.
Ultem
Ultem is a high-performance polymer that offers excellent thermal stability and chemical resistance. Its ability to withstand high temperatures makes it suitable for automotive parts that must endure prolonged exposure to heat, like sensors and manifolds.
Delrin
Delrin, a type of Acetal, is known for its low friction and high stiffness, making it ideal for applications requiring precise, durable parts. In the automotive industry, it’s often used for gears, safety restraint components, and door system parts.
PEEK
PEEK (Polyether Ether Ketone) is highly regarded for its mechanical and chemical resistance properties. In automotive machining, it is used for components that require robustness in high temperature and high-pressure environments, such as seals and bearings in engines.
PTFE
PTFE (Polytetrafluoroethylene), often known as Teflon, is used for its exceptional heat resistance, chemical inertness, and slippery surface. It’s ideal for automotive parts that need to minimize friction, such as in fuel hoses and gaskets.