Machining 4130 steel can feel like a high-stakes game, especially when you’re dealing with parts that require precision, strength, and durability. The challenge? Getting the machining process right without risking tool wear, overheating, or poor surface finish. If you’ve ever had to deal with these issues, you know that understanding 4130 steel’s unique properties is critical to achieving optimal results. Fortunately, I’ve got the tips and tricks you need to master this material and get top-quality parts every time.
4130 steel, a low-alloy chromium-molybdenum steel, is a popular choice in machining due to its strength, toughness, and ability to resist wear. It’s commonly used in industries like aerospace, automotive, and military, where high-performance materials are essential. The key to successful machining of 4130 steel lies in selecting the right tools, optimizing speeds and feeds, and managing heat.
Let’s dive into the nitty-gritty of machining 4130 steel. You’ll learn about the best practices, tools, techniques, and common challenges, so you can handle this material like a pro!
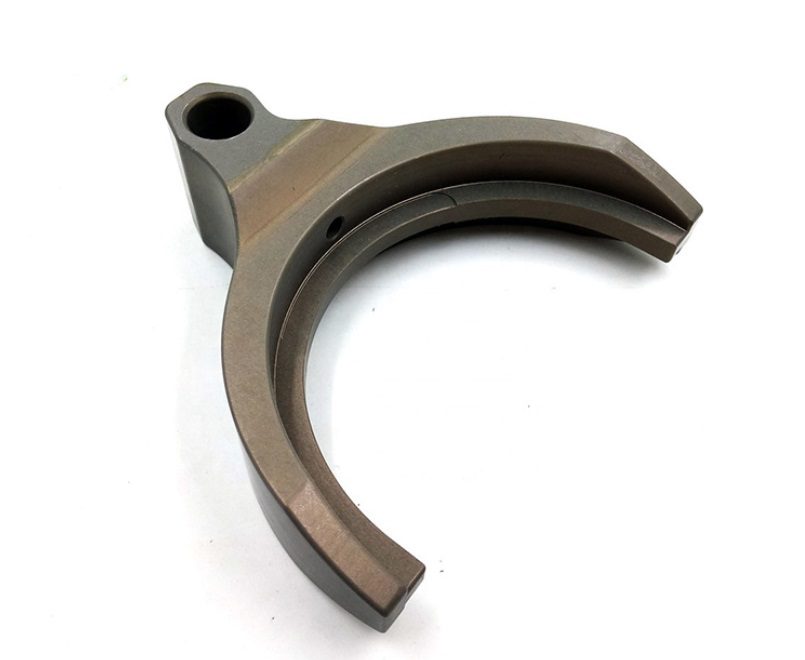