Precision and Tolerances in Phenolic Machining
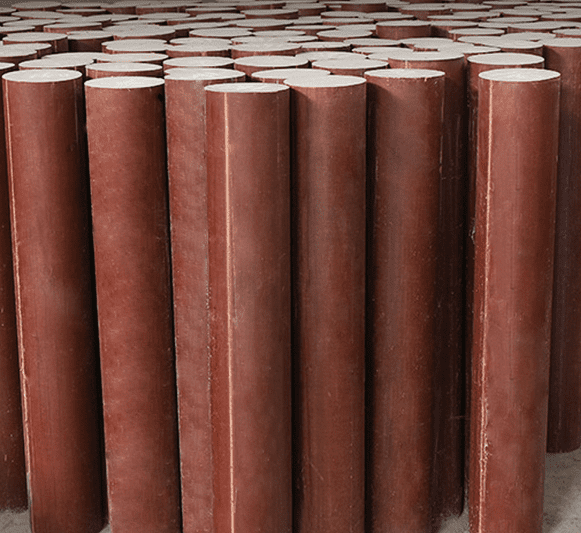
Why Tight Tolerances Matter in Phenolic Parts
Tight tolerances are crucial in phenolic machining because they ensure the parts will function correctly within their specific applications. Phenolic parts are often used in electrical and mechanical systems where even minor deviations can lead to failure or inefficiency.
For example, in aerospace and automotive industries, parts must fit seamlessly and perform under extreme conditions without failure. Tight tolerances ensure that each phenolic component can withstand operational stresses without compromising the system’s integrity.
Achieving Dimensional Accuracy with Advanced Machining Tools
Achieving high dimensional accuracy in phenolic machining requires advanced machining tools and technology. CNC machines, equipped with precision tooling and sophisticated software, can produce parts that adhere closely to specified dimensions.
The use of these advanced tools allows for consistent reproduction of parts, even with complex shapes and thin walls, minimizing material waste and production time. The precision offered by these tools also reduces the need for post-machining adjustments, which can be costly and time-consuming.
Balancing Precision and Cost-Effectiveness in Machining Services
While maintaining high precision is paramount, it is also important to consider the cost-effectiveness of the machining process. This balance is achieved through optimizing machining parameters, selecting appropriate tooling, and employing efficient machining strategies.
For instance, choosing the right type of cutting tool and adjusting the cutting speed and feed rate can minimize tool wear and reduce machining time, thereby lowering the overall production costs. Additionally, leveraging multi-axis CNC machines can reduce the number of setups required, further enhancing efficiency and reducing costs.